What are the Product Standards for Resistor Wiring?
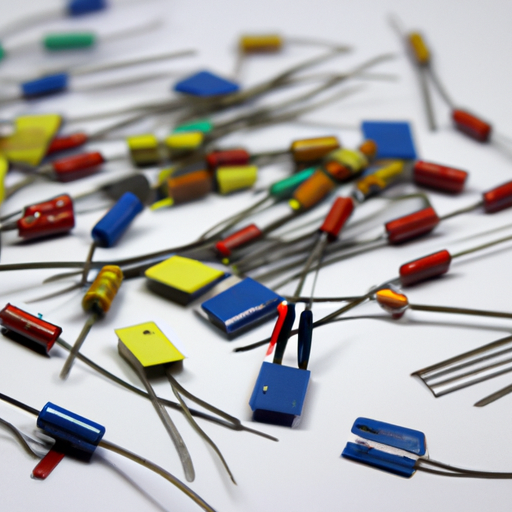
I. Introduction
Resistors are fundamental components in electronic circuits, serving the critical function of controlling current flow and voltage levels. They are essential for ensuring that electronic devices operate correctly and safely. Given their importance, product standards for resistor wiring are crucial. These standards ensure that resistors perform reliably and safely in various applications, from consumer electronics to industrial machinery. This blog post will explore the product standards for resistor wiring, detailing the regulatory bodies involved, key specifications, testing methods, industry applications, and future trends.
II. Understanding Resistor Wiring
A. Basic Principles of Resistors
Resistors are passive electrical components that oppose the flow of electric current, converting electrical energy into heat. They come in various types, including fixed, variable, and specialty resistors, each serving different functions in electronic circuits. The resistance value, measured in ohms, is a critical parameter, as it determines how much current will flow for a given voltage according to Ohm's Law (V = IR). Tolerances, which indicate how much the actual resistance can deviate from the specified value, are also vital for ensuring circuit performance.
B. Wiring Configurations
Resistors can be connected in series or parallel configurations, each affecting the overall resistance and performance of the circuit differently. In a series configuration, the total resistance increases, while in a parallel configuration, the total resistance decreases. Understanding these configurations is essential for designing circuits that meet specific performance criteria.
III. Regulatory Bodies and Standards
A. Overview of Key Organizations
Several organizations play a pivotal role in establishing product standards for resistors and their wiring. The International Electrotechnical Commission (IEC) develops international standards for electrical and electronic technologies. The Institute of Electrical and Electronics Engineers (IEEE) focuses on advancing technology for humanity, including standards for electrical components. The American National Standards Institute (ANSI) oversees the development of voluntary consensus standards for products, services, processes, and systems in the United States.
B. Role of These Organizations in Establishing Standards
These organizations collaborate with industry experts to create and maintain standards that ensure safety, reliability, and interoperability of electrical components, including resistors. Their guidelines help manufacturers produce components that meet the necessary quality and performance criteria, ultimately benefiting consumers and industries alike.
IV. Key Product Standards for Resistor Wiring
A. Electrical Specifications
1. **Resistance Value Tolerances**: Resistors are manufactured with specific resistance values, but due to variations in materials and processes, tolerances are established. Common tolerances include ±1%, ±5%, and ±10%, indicating how much the actual resistance can vary from the nominal value.
2. **Power Ratings and Thermal Management**: Resistors must be rated for the amount of power they can dissipate without overheating. This is typically expressed in watts (W). Proper thermal management is essential to prevent failure, and manufacturers often specify maximum operating temperatures.
3. **Voltage Ratings and Insulation Requirements**: Resistors must also have voltage ratings that indicate the maximum voltage they can handle without breaking down. Insulation materials and techniques are specified to ensure safety and reliability.
B. Mechanical Specifications
1. **Physical Dimensions and Form Factors**: Resistors come in various sizes and shapes, which are defined by industry standards. These specifications ensure compatibility with circuit boards and other components.
2. **Mounting and Connection Standards**: Standards dictate how resistors should be mounted and connected within a circuit. This includes lead spacing, terminal types, and soldering techniques to ensure reliable electrical connections.
C. Environmental Specifications
1. **Temperature Coefficients and Stability**: The temperature coefficient indicates how much a resistor's value changes with temperature. Low-temperature coefficients are preferred for precision applications.
2. **Humidity and Corrosion Resistance**: Resistors must be able to withstand environmental factors such as humidity and corrosive substances. Standards often specify testing methods to ensure reliability under various conditions.
3. **Compliance with RoHS and Other Environmental Regulations**: The Restriction of Hazardous Substances (RoHS) directive limits the use of certain hazardous materials in electrical and electronic equipment. Compliance with such regulations is essential for manufacturers to ensure their products are safe and environmentally friendly.
V. Testing and Quality Assurance
A. Importance of Testing in Resistor Manufacturing
Testing is a critical aspect of resistor manufacturing, ensuring that products meet established standards and perform reliably in their intended applications. Rigorous testing helps identify defects and ensures that resistors can withstand the conditions they will encounter in real-world use.
B. Common Testing Methods
1. **Electrical Testing**: This includes resistance measurement, where the actual resistance is compared to the specified value. Other electrical tests may include voltage and power rating assessments.
2. **Mechanical Testing**: Mechanical tests assess the physical integrity of resistors, including stress and strain analysis to ensure they can withstand mechanical forces during operation.
3. **Environmental Testing**: Environmental tests simulate conditions such as temperature fluctuations, humidity, and exposure to corrosive substances to evaluate how resistors perform under stress.
C. Certification Processes and Compliance Verification
Manufacturers often seek certification from recognized organizations to demonstrate compliance with industry standards. This process involves rigorous testing and documentation to verify that products meet the necessary specifications.
VI. Industry Applications and Implications
A. Use of Resistors in Various Industries
Resistors are ubiquitous in many industries, including:
1. **Consumer Electronics**: Resistors are found in devices such as smartphones, televisions, and computers, where they help regulate current and voltage.
2. **Automotive**: In vehicles, resistors are used in various applications, including sensors, control systems, and lighting.
3. **Telecommunications**: Resistors play a crucial role in communication devices, ensuring signal integrity and proper functioning of circuits.
B. Implications of Non-Compliance with Standards
Failure to comply with product standards can have serious implications, including:
1. **Safety Risks**: Non-compliant resistors may overheat or fail, posing safety hazards to users.
2. **Performance Issues**: Resistors that do not meet specifications can lead to circuit malfunctions, affecting the overall performance of electronic devices.
3. **Legal and Financial Repercussions**: Manufacturers may face legal action, fines, or loss of reputation if their products do not comply with established standards.
VII. Future Trends in Resistor Wiring Standards
A. Advances in Materials and Technology
As technology evolves, new materials and manufacturing techniques are being developed to enhance resistor performance. Innovations such as thin-film resistors and advanced ceramic materials are paving the way for more efficient and reliable components.
B. The Impact of the Internet of Things (IoT) on Resistor Standards
The rise of IoT devices is driving demand for more precise and reliable resistors. As these devices become more interconnected, the need for standardized components that can operate in diverse environments will grow.
C. Evolving Environmental Regulations and Sustainability Considerations
As environmental concerns continue to rise, regulations surrounding hazardous materials and sustainability will likely become more stringent. Manufacturers will need to adapt to these changes by developing eco-friendly products that comply with new standards.
VIII. Conclusion
Product standards for resistor wiring are essential for ensuring the safety, reliability, and performance of electronic devices. By adhering to established specifications and undergoing rigorous testing, manufacturers can produce high-quality resistors that meet the demands of various industries. As technology advances and environmental regulations evolve, the importance of these standards will only increase, shaping the future of resistor technology and its applications.
IX. References
1. International Electrotechnical Commission (IEC) Standards
2. Institute of Electrical and Electronics Engineers (IEEE) Standards
3. American National Standards Institute (ANSI) Standards
4. Relevant academic and industry publications on resistor technology and standards
5. Websites of regulatory bodies and organizations involved in standardization
This comprehensive overview of product standards for resistor wiring highlights the critical role these components play in electronic circuits and the importance of adhering to established guidelines to ensure safety and performance.
What are the Product Standards for Resistor Wiring?
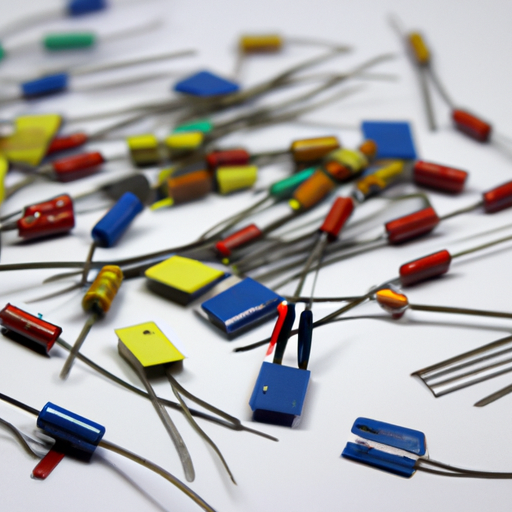
I. Introduction
Resistors are fundamental components in electronic circuits, serving the critical function of controlling current flow and voltage levels. They are essential for ensuring that electronic devices operate correctly and safely. Given their importance, product standards for resistor wiring are crucial. These standards ensure that resistors perform reliably and safely in various applications, from consumer electronics to industrial machinery. This blog post will explore the product standards for resistor wiring, detailing the regulatory bodies involved, key specifications, testing methods, industry applications, and future trends.
II. Understanding Resistor Wiring
A. Basic Principles of Resistors
Resistors are passive electrical components that oppose the flow of electric current, converting electrical energy into heat. They come in various types, including fixed, variable, and specialty resistors, each serving different functions in electronic circuits. The resistance value, measured in ohms, is a critical parameter, as it determines how much current will flow for a given voltage according to Ohm's Law (V = IR). Tolerances, which indicate how much the actual resistance can deviate from the specified value, are also vital for ensuring circuit performance.
B. Wiring Configurations
Resistors can be connected in series or parallel configurations, each affecting the overall resistance and performance of the circuit differently. In a series configuration, the total resistance increases, while in a parallel configuration, the total resistance decreases. Understanding these configurations is essential for designing circuits that meet specific performance criteria.
III. Regulatory Bodies and Standards
A. Overview of Key Organizations
Several organizations play a pivotal role in establishing product standards for resistors and their wiring. The International Electrotechnical Commission (IEC) develops international standards for electrical and electronic technologies. The Institute of Electrical and Electronics Engineers (IEEE) focuses on advancing technology for humanity, including standards for electrical components. The American National Standards Institute (ANSI) oversees the development of voluntary consensus standards for products, services, processes, and systems in the United States.
B. Role of These Organizations in Establishing Standards
These organizations collaborate with industry experts to create and maintain standards that ensure safety, reliability, and interoperability of electrical components, including resistors. Their guidelines help manufacturers produce components that meet the necessary quality and performance criteria, ultimately benefiting consumers and industries alike.
IV. Key Product Standards for Resistor Wiring
A. Electrical Specifications
1. **Resistance Value Tolerances**: Resistors are manufactured with specific resistance values, but due to variations in materials and processes, tolerances are established. Common tolerances include ±1%, ±5%, and ±10%, indicating how much the actual resistance can vary from the nominal value.
2. **Power Ratings and Thermal Management**: Resistors must be rated for the amount of power they can dissipate without overheating. This is typically expressed in watts (W). Proper thermal management is essential to prevent failure, and manufacturers often specify maximum operating temperatures.
3. **Voltage Ratings and Insulation Requirements**: Resistors must also have voltage ratings that indicate the maximum voltage they can handle without breaking down. Insulation materials and techniques are specified to ensure safety and reliability.
B. Mechanical Specifications
1. **Physical Dimensions and Form Factors**: Resistors come in various sizes and shapes, which are defined by industry standards. These specifications ensure compatibility with circuit boards and other components.
2. **Mounting and Connection Standards**: Standards dictate how resistors should be mounted and connected within a circuit. This includes lead spacing, terminal types, and soldering techniques to ensure reliable electrical connections.
C. Environmental Specifications
1. **Temperature Coefficients and Stability**: The temperature coefficient indicates how much a resistor's value changes with temperature. Low-temperature coefficients are preferred for precision applications.
2. **Humidity and Corrosion Resistance**: Resistors must be able to withstand environmental factors such as humidity and corrosive substances. Standards often specify testing methods to ensure reliability under various conditions.
3. **Compliance with RoHS and Other Environmental Regulations**: The Restriction of Hazardous Substances (RoHS) directive limits the use of certain hazardous materials in electrical and electronic equipment. Compliance with such regulations is essential for manufacturers to ensure their products are safe and environmentally friendly.
V. Testing and Quality Assurance
A. Importance of Testing in Resistor Manufacturing
Testing is a critical aspect of resistor manufacturing, ensuring that products meet established standards and perform reliably in their intended applications. Rigorous testing helps identify defects and ensures that resistors can withstand the conditions they will encounter in real-world use.
B. Common Testing Methods
1. **Electrical Testing**: This includes resistance measurement, where the actual resistance is compared to the specified value. Other electrical tests may include voltage and power rating assessments.
2. **Mechanical Testing**: Mechanical tests assess the physical integrity of resistors, including stress and strain analysis to ensure they can withstand mechanical forces during operation.
3. **Environmental Testing**: Environmental tests simulate conditions such as temperature fluctuations, humidity, and exposure to corrosive substances to evaluate how resistors perform under stress.
C. Certification Processes and Compliance Verification
Manufacturers often seek certification from recognized organizations to demonstrate compliance with industry standards. This process involves rigorous testing and documentation to verify that products meet the necessary specifications.
VI. Industry Applications and Implications
A. Use of Resistors in Various Industries
Resistors are ubiquitous in many industries, including:
1. **Consumer Electronics**: Resistors are found in devices such as smartphones, televisions, and computers, where they help regulate current and voltage.
2. **Automotive**: In vehicles, resistors are used in various applications, including sensors, control systems, and lighting.
3. **Telecommunications**: Resistors play a crucial role in communication devices, ensuring signal integrity and proper functioning of circuits.
B. Implications of Non-Compliance with Standards
Failure to comply with product standards can have serious implications, including:
1. **Safety Risks**: Non-compliant resistors may overheat or fail, posing safety hazards to users.
2. **Performance Issues**: Resistors that do not meet specifications can lead to circuit malfunctions, affecting the overall performance of electronic devices.
3. **Legal and Financial Repercussions**: Manufacturers may face legal action, fines, or loss of reputation if their products do not comply with established standards.
VII. Future Trends in Resistor Wiring Standards
A. Advances in Materials and Technology
As technology evolves, new materials and manufacturing techniques are being developed to enhance resistor performance. Innovations such as thin-film resistors and advanced ceramic materials are paving the way for more efficient and reliable components.
B. The Impact of the Internet of Things (IoT) on Resistor Standards
The rise of IoT devices is driving demand for more precise and reliable resistors. As these devices become more interconnected, the need for standardized components that can operate in diverse environments will grow.
C. Evolving Environmental Regulations and Sustainability Considerations
As environmental concerns continue to rise, regulations surrounding hazardous materials and sustainability will likely become more stringent. Manufacturers will need to adapt to these changes by developing eco-friendly products that comply with new standards.
VIII. Conclusion
Product standards for resistor wiring are essential for ensuring the safety, reliability, and performance of electronic devices. By adhering to established specifications and undergoing rigorous testing, manufacturers can produce high-quality resistors that meet the demands of various industries. As technology advances and environmental regulations evolve, the importance of these standards will only increase, shaping the future of resistor technology and its applications.
IX. References
1. International Electrotechnical Commission (IEC) Standards
2. Institute of Electrical and Electronics Engineers (IEEE) Standards
3. American National Standards Institute (ANSI) Standards
4. Relevant academic and industry publications on resistor technology and standards
5. Websites of regulatory bodies and organizations involved in standardization
This comprehensive overview of product standards for resistor wiring highlights the critical role these components play in electronic circuits and the importance of adhering to established guidelines to ensure safety and performance.