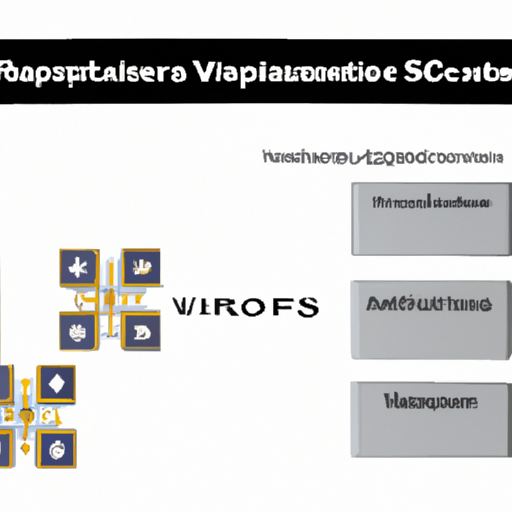
Application Development in Variable Capacitance (Varicaps, Varactors) for CFR-25JB-52-1R8: Key Technologies and Success StoriesVariable capacitance diodes, commonly referred to as varicaps or varactors, are essential components in modern electronic systems, particularly in RF and microwave applications. The CFR-25JB-52-1R8 is a specific varactor diode that exemplifies the advancements in this technology. Below, we explore key technologies that have driven the development of varactors and highlight notable success stories in their application.
Key Technologies in Varactor Development1. Material Science Advances2. Integrated Circuit (IC) Design3. Tuning Techniques4. Simulation and Modeling5. Packaging Innovations1. Mobile Communication2. Television Tuners3. Phase-Locked Loops (PLLs)4. Automotive Applications5. Consumer Electronics6. Aerospace and Defense Success Stories in Varactor Applications ConclusionThe development of variable capacitance diodes, such as the CFR-25JB-52-1R8, has significantly influenced various industries, from telecommunications to automotive and consumer electronics. As technology continues to evolve, the integration of varactors into more complex systems, along with ongoing research into new materials and designs, promises to yield even more innovative applications and success stories in the future. The versatility and adaptability of varactors ensure their continued relevance in the ever-changing landscape of electronic technology.
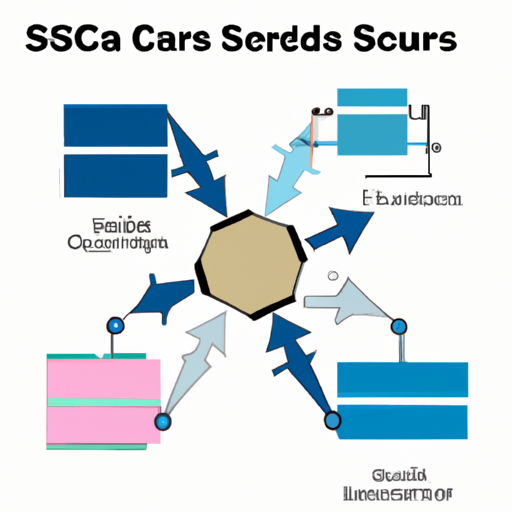
Overview of DIACs and SIDACsDIACs (Diodes for Alternating Current) and SIDACs (Silicon Diodes for Alternating Current) are essential semiconductor devices used primarily for controlling and switching applications in AC circuits. Their unique characteristics make them suitable for a variety of applications, including light dimming, motor speed control, and over-voltage protection. Below, we delve into the core functional technology of these devices and explore several application development cases that highlight their effectiveness.
Core Functional Technology 1. DIAC (Diode for Alternating Current)
- **Structure**: A DIAC is a two-terminal device that exhibits a breakover voltage. It remains in a non-conducting state until the voltage across it exceeds a specific threshold, at which point it switches to a conducting state.
- **Operation**: The DIAC features symmetrical breakdown characteristics, allowing it to conduct in both directions. This property makes it particularly suitable for AC applications.
- **Applications**: Commonly used in phase control applications, such as light dimmers and motor speed controllers. It can also serve as a triggering device for TRIACs, which control AC loads. 2. SIDAC (Silicon Diode for Alternating Current)
- **Structure**: Similar to a DIAC, a SIDAC is a two-terminal device designed to handle higher power levels, featuring a more robust construction.
- **Operation**: The SIDAC also has a breakover voltage and switches from a non-conducting to a conducting state when the voltage exceeds a certain level. It is often employed in applications requiring high voltage and current handling.
- **Applications**: Used in over-voltage protection circuits, snubber circuits, and as a trigger device for other power semiconductor devices. Application Development Cases 1. Light Dimming Applications
- **Description**: DIACs are extensively used in light dimmers to control the brightness of incandescent lamps. By integrating a DIAC with a TRIAC, the phase angle of the AC voltage can be modulated, enabling smooth dimming.
- **Development Case**: A manufacturer developed a smart dimmer switch that utilizes a DIAC to control the phase angle of the AC supply to LED lights, resulting in energy savings and extended lamp life. This innovation allows users to adjust brightness levels seamlessly, enhancing user experience. 2. Motor Speed Control
- **Description**: SIDACs are effective in motor speed control applications, where they help regulate the voltage supplied to the motor, thus controlling its speed.
- **Development Case**: An industrial automation company designed a motor control system using SIDACs to manage the speed of AC motors in conveyor systems. This implementation improved operational efficiency and reduced energy consumption, showcasing the benefits of precise motor control in industrial settings. 3. Over-Voltage Protection
- **Description**: SIDACs are instrumental in protecting sensitive electronic components from voltage spikes. They can be integrated into surge protection devices to clamp excessive voltages.
- **Development Case**: A consumer electronics company incorporated SIDACs into their power supply units to safeguard against voltage transients. This enhancement significantly improved the reliability and longevity of their products, ensuring customer satisfaction and reducing warranty claims. 4. Snubber Circuits
- **Description**: Both DIACs and SIDACs can be utilized in snubber circuits to protect switching devices from voltage spikes caused by inductive loads.
- **Development Case**: An engineering firm developed a snubber circuit using a DIAC to protect a TRIAC in a heating control application. This design ensured stable operation and prolonged the life of the components, demonstrating the importance of protective measures in electronic designs. 5. Triggering TRIACs
- **Description**: DIACs are frequently employed to trigger TRIACs in AC control applications. The DIAC provides a sharp switching action, ideal for triggering the TRIAC at the desired phase angle.
- **Development Case**: A lighting control system was designed using a DIAC to trigger a TRIAC for controlling the brightness of stage lighting. This application allowed for precise control during performances, enhancing the overall production quality. ConclusionDIACs and SIDACs are versatile components that play a crucial role in various AC control applications. Their ability to handle high voltages and currents, combined with their fast switching capabilities, makes them ideal for use in light dimmers, motor controls, and protection circuits. As technology continues to advance, the integration of these devices into smart systems and IoT applications is expected to increase, further enhancing their utility in modern electronic designs. The ongoing development of innovative applications will likely lead to new opportunities for DIACs and SIDACs in the evolving landscape of electronics.
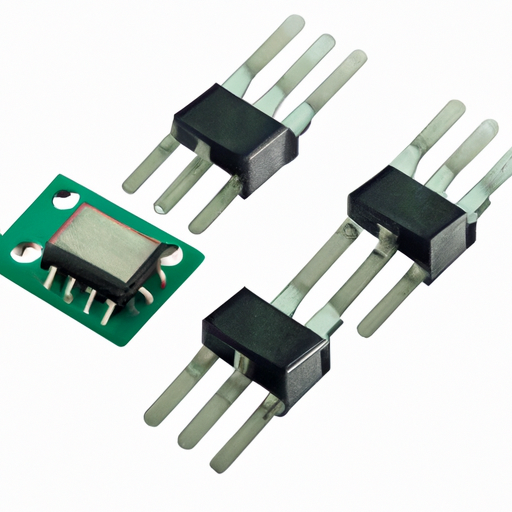
Application Development in Pin Configurable/Selectable Oscillators for CFR-25JB-52-1M6: Key Technologies and Success StoriesPin configurable/selectable oscillators, such as the CFR-25JB-52-1M6, play a crucial role in modern electronic design by offering flexibility, efficiency, and reliability. This overview highlights the key technologies that underpin these oscillators and showcases successful implementations across various industries.
Key Technologies1. Pin Configuration and Selection2. Low Power Consumption3. High Stability and Accuracy4. Integrated Circuit Technology5. Programmability6. Robustness and Reliability1. Telecommunications2. Consumer Electronics3. Automotive Applications4. Industrial Automation5. Medical Devices Success Stories ConclusionThe CFR-25JB-52-1M6 and similar pin configurable/selectable oscillators represent a significant advancement in oscillator technology, offering flexibility, reliability, and efficiency across various applications. Their successful implementation in telecommunications, consumer electronics, automotive, industrial automation, and medical devices underscores their versatility and importance in modern electronic design. As technology continues to evolve, the role of these oscillators is expected to expand, driving further innovation across multiple sectors and enhancing the functionality of next-generation electronic devices.
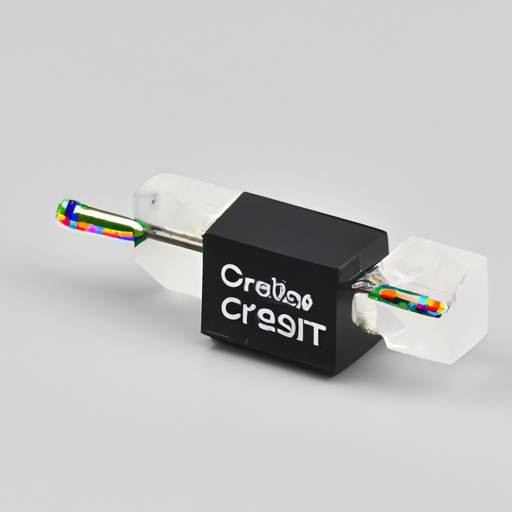
Overview of Crystal, Oscillator, and Resonator AccessoriesCrystal oscillators, resonators, and their accessories are fundamental components in electronic circuits, providing stable frequency references essential for timing and synchronization. The CFR-50JB-52-1M6 is a specific model of crystal oscillator that exemplifies the capabilities of this technology. Below, we delve into the core functional technologies, applications, and development cases related to crystal oscillators and their accessories.
Core Functional Technologies1. Frequency Stability 2. Low Phase Noise 3. Temperature Compensation 4. Miniaturization 5. Power Efficiency 1. Consumer Electronics2. Telecommunications3. Automotive Applications4. Industrial Automation5. Medical Devices Application Development Cases ConclusionThe CFR-50JB-52-1M6 crystal oscillator and its accessories represent a vital technology in modern electronics, enabling a wide range of applications across various industries. The advancements in frequency stability, low phase noise, temperature compensation, miniaturization, and power efficiency have made crystal oscillators indispensable in today's high-tech landscape. As technology continues to evolve, the role of crystal oscillators will expand, driving innovation in consumer electronics, telecommunications, automotive, industrial automation, and medical devices. The ongoing development of these technologies will further enhance their capabilities, ensuring they meet the demands of future applications.
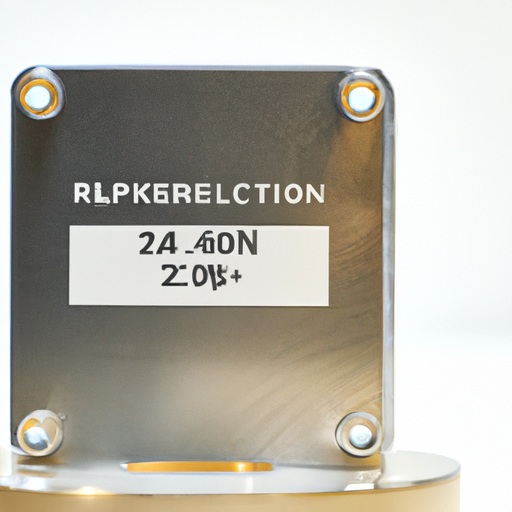
Application Development in Resonators for CFR-25JB-52-1K6: Key Technologies and Success StoriesApplication development in resonators, particularly for components like the CFR-25JB-52-1K6 resistor, involves leveraging various key technologies and methodologies to enhance performance, reliability, and efficiency. While the CFR-25JB-52-1K6 is primarily a resistor, the principles of application development in electronic components can be broadly applied to resonators and other related technologies.
Key Technologies in Application Development for Resonators1. Material Science2. Simulation and Modeling3. Microfabrication Techniques4. Integrated Circuit (IC) Design5. Wireless Communication Technologies6. Digital Signal Processing (DSP)7. Machine Learning and AI1. Telecommunications2. Consumer Electronics3. Automotive Industry4. Medical Devices5. Industrial Applications Success Stories in Resonator Application Development ConclusionThe development of applications involving resonators, such as the CFR-25JB-52-1K6, is a multidisciplinary effort that combines material science, advanced manufacturing techniques, and cutting-edge technologies. Success stories across various industries highlight the importance of resonators in enhancing performance and enabling new functionalities in electronic devices. As technology continues to evolve, the role of resonators will likely expand, leading to innovative applications and solutions that address the growing demands of modern electronics.
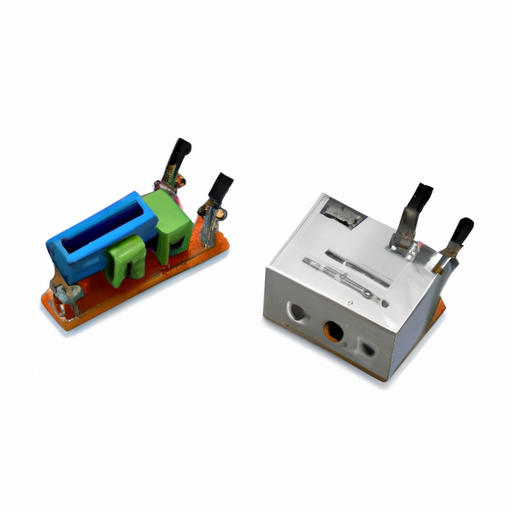
Overview of CFR-25JB-52-1R5 Switching Converter and SMPS TransformersThe CFR-25JB-52-1R5 is a specific model of a switching converter transformer, integral to switch-mode power supplies (SMPS). These transformers play a crucial role in power electronics, facilitating efficient energy conversion and regulation across various applications. Below, we delve into the core functional technologies and notable application development cases that highlight the effectiveness of switching converters and SMPS transformers.
Core Functional Technologies1. Magnetic Core Design2. Winding Techniques3. Switching Frequency4. Feedback and Control Circuits5. Thermal Management1. Consumer Electronics2. Telecommunications3. Industrial Automation4. Renewable Energy Systems5. Electric Vehicles (EVs) Application Development Cases ConclusionThe CFR-25JB-52-1R5 switching converter transformer exemplifies the advancements in SMPS technology, focusing on efficiency, size reduction, and thermal management. Its applications span various industries, from consumer electronics to renewable energy, showcasing the versatility and importance of switching converters in modern power systems. As technology continues to evolve, ongoing research and development will further enhance the capabilities and applications of SMPS transformers, driving innovation in power electronics.
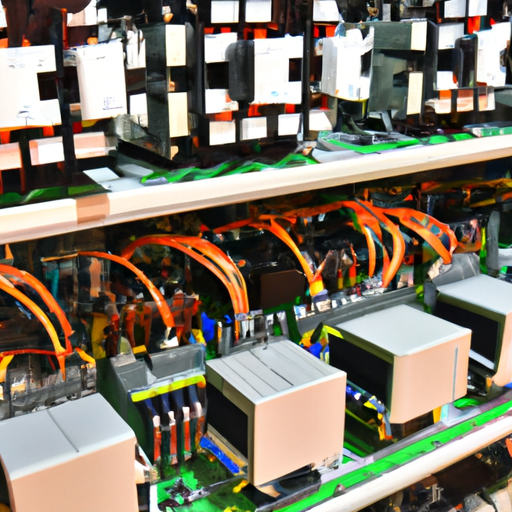
Application Development in Isolation Transformers and Autotransformers: CFR-25JB-52-1M5The development and application of isolation transformers and autotransformers, particularly models like the CFR-25JB-52-1M5, are pivotal in enhancing electrical safety, efficiency, and performance across various sectors. Below is a detailed exploration of the key technologies, functionalities, and notable success stories associated with these transformers.
Key Technologies1. Isolation Transformers2. Autotransformers3. Step-Up and Step-Down Transformers4. CFR-25JB-52-1M5 Specifics1. Medical Equipment2. Industrial Automation3. Renewable Energy Systems4. Telecommunications5. Consumer Electronics Success Stories ConclusionThe development and application of isolation transformers and autotransformers, including models like the CFR-25JB-52-1M5, are integral to modern electrical systems across various industries. Their ability to enhance safety, efficiency, and reliability is underscored by numerous success stories in medical, industrial, renewable energy, telecommunications, and consumer electronics sectors. As technology advances, the role of these transformers is expected to expand, incorporating innovations in materials and design to meet the evolving demands of diverse applications. The ongoing evolution in transformer technology will likely lead to even greater efficiencies and capabilities, further solidifying their importance in the electrical landscape.
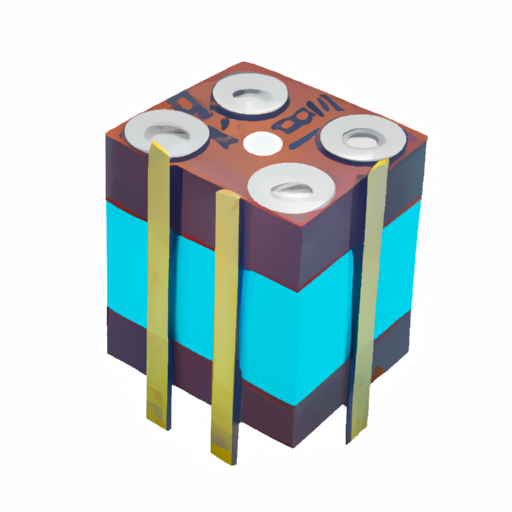
Overview of CFR-50JB-52-1M5 Pulse TransformersThe CFR-50JB-52-1M5 pulse transformer is a specialized device designed to transmit electrical pulses with high fidelity and efficiency. Its design and construction are tailored to meet the demands of various high-frequency applications, making it a critical component in modern electronic systems. Below, we delve deeper into the core functional technologies and application development cases that highlight the significance of pulse transformers like the CFR-50JB-52-1M5.
Core Functional Technologies1. High-Frequency Operation2. Magnetic Core Materials3. Winding Techniques4. Insulation and Dielectric Strength5. Temperature Stability1. Telecommunications2. Switching Power Supplies3. Medical Equipment4. Industrial Automation5. High-Voltage Applications6. Consumer Electronics Application Development Cases ConclusionThe CFR-50JB-52-1M5 pulse transformer exemplifies the advanced technology and diverse applications of pulse transformers in various fields. By focusing on high-frequency operation, optimal core materials, and innovative winding techniques, these transformers play a crucial role in modern electronic systems. Their versatility and reliability make them indispensable in telecommunications, power electronics, medical devices, and more. As technology continues to evolve, the development of pulse transformers will likely expand, leading to new applications and improved performance characteristics, further solidifying their importance in the electronic landscape.
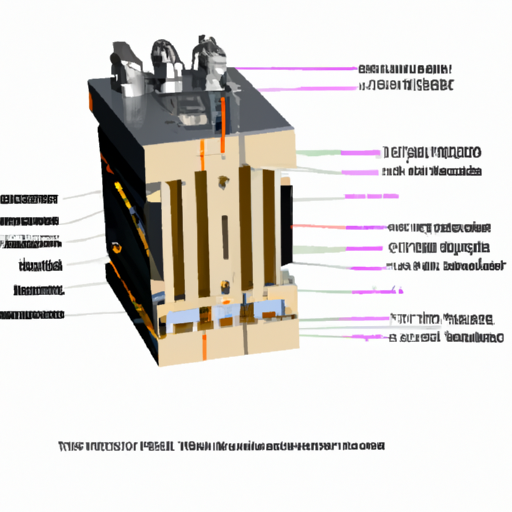
Overview of CFR-50JB-52-1K5 Power TransformerThe CFR-50JB-52-1K5 power transformer, while not extensively documented, represents a specific model within the broader category of power transformers. These devices are critical components in electrical power systems, facilitating the transmission and distribution of electricity across various applications. Below is a detailed exploration of the core functional technologies and application development cases relevant to power transformers, including insights that may apply to the CFR-50JB-52-1K5 model.
Core Functional Technologies of Power Transformers1. Magnetic Core Design2. Winding Configuration3. Cooling Systems4. Tap Changer Mechanisms5. Protection Systems1. Renewable Energy Integration2. Smart Grid Technologies3. Industrial Applications4. Urban Infrastructure5. Electric Vehicle Charging Stations6. Data Centers Application Development Cases ConclusionThe CFR-50JB-52-1K5 power transformer, like other power transformers, plays a vital role in modern electrical systems, enabling efficient power distribution and facilitating the integration of renewable energy sources. Advances in technology, such as smart grid integration and improved cooling systems, continue to enhance the performance and application scope of power transformers. Understanding these core technologies and application cases is essential for engineers and stakeholders involved in power systems design and operation, ensuring that transformers meet the evolving demands of the electrical grid.
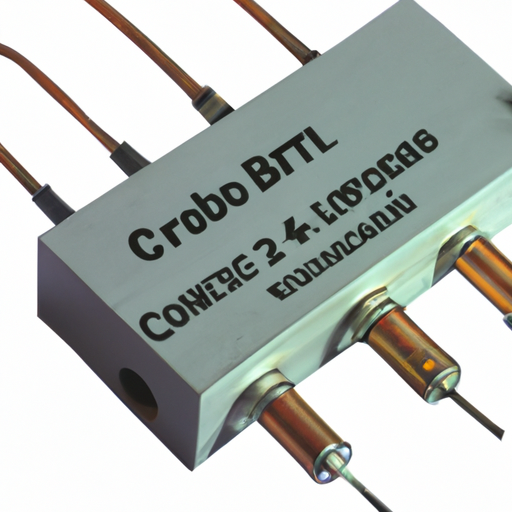
Overview of CFR-50JB-52-1R5 Audio TransformersThe CFR-50JB-52-1R5 is a specialized audio transformer designed for a variety of audio applications, including professional audio equipment, musical instruments, and consumer electronics. Audio transformers are essential components in audio systems, serving multiple functions such as isolating signals, matching impedance, and transforming audio signals to ensure optimal performance.
Core Functional Technology of Audio Transformers1. Impedance Matching 2. Signal Isolation 3. Voltage Transformation 4. Frequency Response 5. Low Distortion 1. Professional Audio Equipment 2. Guitar Amplifiers 3. Broadcasting 4. Consumer Electronics 5. Musical Instruments Application Development Cases ConclusionThe CFR-50JB-52-1R5 audio transformer exemplifies the critical role that audio transformers play in modern audio systems. By providing essential functions such as impedance matching, signal isolation, voltage transformation, and maintaining low distortion, these transformers are indispensable for achieving high-quality audio performance across a wide range of applications. Whether in professional audio, broadcasting, or consumer electronics, the effective use of audio transformers can significantly enhance the overall audio experience, making them a vital component in the design and development of audio systems.
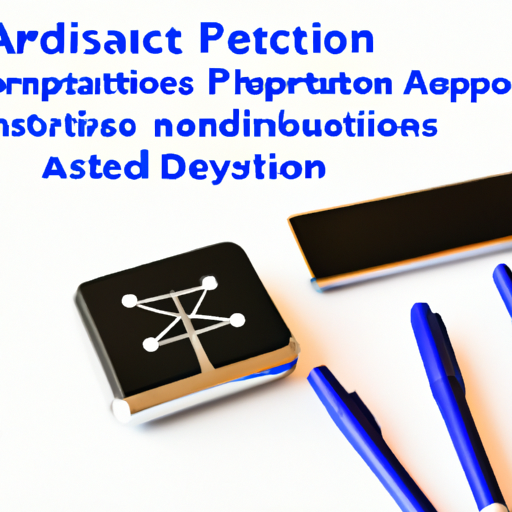
Application Development in Accessories for LT1213CS8: Key Technologies and Success StoriesThe LT1213CS8, a mobile impact crusher from Metso Outotec, is a vital tool in the construction and demolition industry, particularly for recycling materials. The development of accessories for this machinery is crucial for enhancing its functionality, efficiency, and safety. Below, we explore key technologies and notable success stories that illustrate the impact of these advancements.
Key Technologies1. Telematics and IoT Integration2. Advanced Control Systems3. Wearable Technology4. Enhanced Crushing Technology5. Sustainability Innovations1. Case Study: Urban Construction Projects2. Recycling Facility Implementation3. Safety Enhancements4. Sustainable Operations Success Stories ConclusionThe development of accessories for the LT1213CS8 is driven by advancements in technology that enhance performance, safety, and sustainability. Success stories from various sectors underscore the importance of these innovations in improving operational efficiency and meeting contemporary environmental standards. As technology continues to evolve, the potential for further advancements in application development for machinery like the LT1213CS8 remains promising, paving the way for a more efficient and sustainable future in the construction and demolition industry.

Application Development in Value Display Potentiometers for CFR-25JB-52-1K3: Key Technologies and Success StoriesValue Display Potentiometers, such as the CFR-25JB-52-1K3, play a crucial role in electronic applications that require precise resistance control. These components are widely utilized across various sectors, including audio equipment, industrial controls, and consumer electronics. Below is an overview of the key technologies and notable success stories associated with the application development of these potentiometers.
Key Technologies1. Digital Potentiometers2. Analog Potentiometers3. Multi-turn Potentiometers4. Taper Types5. Robustness and Reliability6. Integration with IoT1. Audio Equipment2. Industrial Automation3. Consumer Electronics4. Medical Devices5. Automotive Applications Success Stories ConclusionThe application development of Value Display Potentiometers, particularly the CFR-25JB-52-1K3, highlights the significance of precision, reliability, and adaptability across various industries. As technology continues to advance, the integration of these components with digital systems and IoT is expected to expand their applications, paving the way for further innovations and success stories in the field. The ongoing evolution of potentiometer technology will likely lead to enhanced functionalities and new opportunities in diverse sectors, reinforcing their importance in modern electronic design.
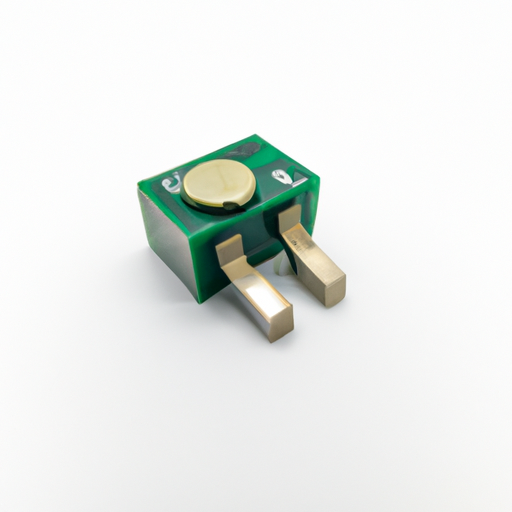
Core Functional Technologies of Trimmer Potentiometers1. Adjustable Resistance: Trimmer potentiometers, such as the CFR-50JB-52-1K3, offer a variable resistance that can be manually adjusted. This feature is essential for calibrating circuits, allowing engineers to set precise voltage levels or current flows, which is critical in applications requiring fine-tuning.
2. Compact Design: The CFR-50JB-52-1K3 is engineered with a compact footprint, making it ideal for space-constrained applications. Its small size allows for seamless integration into various electronic devices without occupying excessive space, which is particularly beneficial in portable electronics. 3. Durability and Reliability: Built to endure repeated adjustments, trimmer potentiometers in the CFR series are known for their robust construction. This durability ensures long-term reliability, even in demanding environmental conditions, making them suitable for both consumer and industrial applications.
4. Temperature Stability: Many trimmer potentiometers, including the CFR-50JB-52-1K3, maintain their resistance values across a wide temperature range. This characteristic is crucial for applications that operate in varying thermal environments, ensuring consistent performance.
5. Low Noise Operation: Designed to minimize electrical noise, trimmer potentiometers are essential in sensitive applications such as audio equipment and precision measurement devices. The low noise operation helps maintain signal integrity, which is vital for high-quality performance.
Application Development Cases1. Audio Equipment Calibration: In high-fidelity audio amplifiers, trimmer potentiometers like the CFR-50JB-52-1K3 are used to adjust gain levels. This fine-tuning capability ensures optimal sound quality and prevents distortion, enhancing the listening experience.
2. Sensor Calibration: Trimmer potentiometers are instrumental in calibrating sensor outputs, such as those from temperature or pressure sensors. By adjusting the resistance, engineers can align the sensor output with expected values, thereby improving measurement accuracy in various systems.
3. Power Supply Regulation: In power supply circuits, trimmer potentiometers are frequently employed to set output voltages. For instance, in a DC-DC converter, the CFR-50JB-52-1K3 can be adjusted to achieve the desired output voltage, providing flexibility in design and application.
4. Feedback Control Systems: In robotics and automation, trimmer potentiometers can be utilized to set reference levels for feedback loops. This precision is crucial for maintaining performance in control systems, ensuring that devices operate within desired parameters.
5. Consumer Electronics: Trimmer potentiometers are commonly found in consumer devices like televisions and radios, where they are used to adjust tuning and volume levels. The CFR-50JB-52-1K3 can be integrated into these devices, allowing users to customize their experience easily.
6. Test Equipment: In laboratory environments, trimmer potentiometers are often used in test equipment to calibrate instruments. For example, in oscilloscopes or multimeters, they can be adjusted to enhance measurement accuracy, ensuring reliable and precise results.
ConclusionTrimmer potentiometers, exemplified by the CFR-50JB-52-1K3, are integral components in modern electronics, providing adjustable resistance for calibration and fine-tuning across a multitude of applications. Their compact design, durability, and low noise operation make them suitable for diverse uses, ranging from consumer electronics to industrial applications. As technology advances, the demand for precise control and calibration will continue to grow, reinforcing the significance of trimmer potentiometers in future electronic developments.