What Product Types Do Resistor Factories Include?
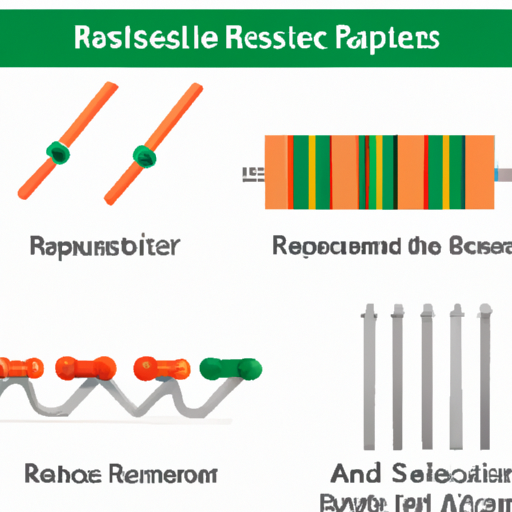
I. Introduction
Resistors are fundamental components in electronic circuits, serving the critical function of controlling the flow of electric current. By providing resistance, they help to manage voltage levels, protect sensitive components, and ensure the proper functioning of electronic devices. The resistor manufacturing industry plays a vital role in the electronics sector, producing a wide variety of resistor types to meet the diverse needs of various applications. This blog post will explore the different product types that resistor factories include, the manufacturing processes involved, their applications, and the latest trends in the industry.
II. Types of Resistors
Resistors can be broadly categorized into three main types: fixed resistors, variable resistors, and specialty resistors. Each category encompasses various subtypes, each designed for specific applications and performance requirements.
A. Fixed Resistors
Fixed resistors are the most common type, providing a constant resistance value. They are widely used in electronic circuits for various purposes.
1. **Carbon Composition Resistors**: Made from a mixture of carbon and a binding material, these resistors are known for their high energy absorption and ability to withstand high temperatures. However, they have a relatively high tolerance and are less stable than other types.
2. **Carbon Film Resistors**: These resistors are made by depositing a thin layer of carbon on a ceramic substrate. They offer better stability and lower noise compared to carbon composition resistors, making them suitable for audio applications.
3. **Metal Film Resistors**: Constructed from a thin film of metal, these resistors provide high precision and low temperature coefficients. They are commonly used in applications requiring high accuracy, such as in measurement devices.
4. **Wirewound Resistors**: These resistors are made by winding a metal wire around a ceramic or fiberglass core. They can handle high power levels and are often used in power applications, such as in power supplies and amplifiers.
5. **Thick Film Resistors**: Made by printing a thick layer of resistive material onto a substrate, these resistors are cost-effective and suitable for surface mount technology (SMT). They are widely used in consumer electronics.
6. **Thin Film Resistors**: Similar to thick film resistors but with a thinner layer of resistive material, thin film resistors offer higher precision and stability. They are often used in high-frequency applications.
B. Variable Resistors
Variable resistors allow for adjustable resistance values, making them versatile components in electronic circuits.
1. **Potentiometers**: These are three-terminal devices that can adjust voltage levels in a circuit. They are commonly used in volume controls, tuning circuits, and other applications where variable resistance is needed.
2. **Rheostats**: A type of variable resistor, rheostats are used to control current flow in a circuit. They are often employed in applications requiring high power, such as in lighting controls and motor speed adjustments.
C. Specialty Resistors
Specialty resistors are designed for specific applications and often have unique characteristics.
1. **Precision Resistors**: These resistors have tight tolerance levels and are used in applications where accuracy is critical, such as in instrumentation and measurement devices.
2. **High-Voltage Resistors**: Designed to withstand high voltage levels, these resistors are used in applications such as power supplies and high-voltage testing equipment.
3. **High-Power Resistors**: Capable of dissipating significant amounts of power, high-power resistors are used in applications like power amplifiers and industrial equipment.
4. **Current Sensing Resistors**: These resistors are used to measure current flow in a circuit. They are often employed in power management systems and battery monitoring applications.
5. **Thermistors**: Temperature-sensitive resistors, thermistors change resistance with temperature variations. They are commonly used in temperature sensing and control applications.
6. **Varistors**: Voltage-dependent resistors, varistors protect circuits from voltage spikes by changing resistance based on the applied voltage. They are often used in surge protection devices.
7. **Photoresistors**: Also known as light-dependent resistors (LDRs), these resistors change resistance based on light exposure. They are commonly used in light-sensing applications, such as automatic lighting systems.
III. Manufacturing Processes
The manufacturing of resistors involves several key processes, from material selection to quality control.
A. Overview of the Resistor Manufacturing Process
The resistor manufacturing process typically begins with the selection of appropriate materials, followed by the fabrication of the resistive element, and finally, the assembly and testing of the finished product. Each step is crucial to ensure the performance and reliability of the resistors.
B. Materials Used in Resistor Production
1. **Conductive Materials**: The choice of conductive materials is critical in determining the resistance value and performance of the resistor. Common materials include carbon, metal films, and metal wires.
2. **Insulating Materials**: Insulating materials are used to encase the resistive element and prevent short circuits. Common insulating materials include ceramics, plastics, and glass.
C. Quality Control Measures in Resistor Manufacturing
Quality control is essential in resistor manufacturing to ensure that products meet industry standards and specifications. This includes testing for resistance values, temperature coefficients, and tolerance levels. Manufacturers often employ automated testing equipment to streamline the quality assurance process.
IV. Applications of Resistors
Resistors are used in a wide range of applications across various industries, highlighting their versatility and importance.
A. Consumer Electronics
In consumer electronics, resistors are used in devices such as televisions, smartphones, and computers to control current flow, manage voltage levels, and protect sensitive components.
B. Automotive Industry
In the automotive industry, resistors play a crucial role in electronic control systems, sensors, and lighting systems, ensuring the proper functioning of modern vehicles.
C. Industrial Equipment
Resistors are used in industrial equipment for power management, motor control, and automation systems, contributing to the efficiency and reliability of manufacturing processes.
D. Telecommunications
In telecommunications, resistors are essential for signal processing, impedance matching, and circuit protection, enabling reliable communication systems.
E. Medical Devices
In medical devices, precision resistors are used in diagnostic equipment, monitoring systems, and therapeutic devices, ensuring accurate measurements and safe operation.
V. Trends in Resistor Manufacturing
The resistor manufacturing industry is evolving, driven by technological advancements and changing market demands.
A. Technological Advancements
Innovations in materials and manufacturing techniques are leading to the development of more efficient and reliable resistors. For example, advancements in thin film technology are enabling the production of smaller, more precise resistors.
B. Demand for Miniaturization
As electronic devices become smaller and more compact, there is a growing demand for miniaturized resistors. Manufacturers are responding by developing smaller form factors and surface mount technology (SMT) resistors.
C. Environmental Considerations
With increasing awareness of environmental issues, resistor manufacturers are focusing on sustainable practices, such as using eco-friendly materials and reducing waste in the production process.
D. Custom Resistor Solutions
As industries seek tailored solutions for specific applications, there is a rising demand for custom resistor designs. Manufacturers are increasingly offering bespoke resistor solutions to meet unique performance requirements.
VI. Conclusion
Resistors are indispensable components in modern electronics, playing a vital role in controlling current flow and ensuring the proper functioning of devices across various industries. The resistor manufacturing industry encompasses a wide range of product types, from fixed and variable resistors to specialty resistors, each designed for specific applications. As technology continues to advance, the industry is evolving to meet the demands for miniaturization, precision, and sustainability. The future outlook for resistor factories is promising, with ongoing innovations and a growing emphasis on custom solutions, ensuring that resistors will remain a cornerstone of electronic design and manufacturing.
VII. References
1. Academic journals on electronics and materials science.
2. Industry reports from market research firms.
3. Manufacturer websites for product specifications and innovations.
4. Technical manuals and guides on resistor technology and applications.
What Product Types Do Resistor Factories Include?
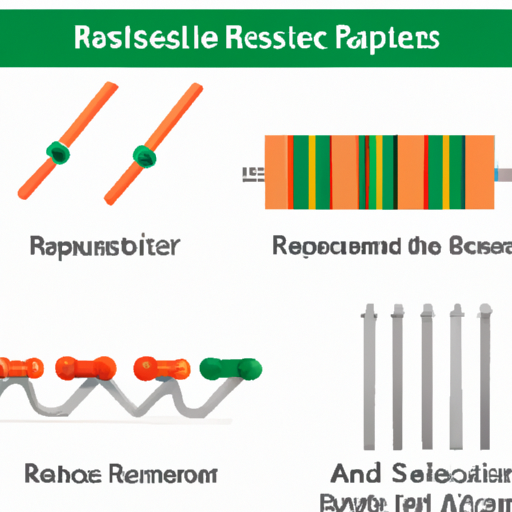
I. Introduction
Resistors are fundamental components in electronic circuits, serving the critical function of controlling the flow of electric current. By providing resistance, they help to manage voltage levels, protect sensitive components, and ensure the proper functioning of electronic devices. The resistor manufacturing industry plays a vital role in the electronics sector, producing a wide variety of resistor types to meet the diverse needs of various applications. This blog post will explore the different product types that resistor factories include, the manufacturing processes involved, their applications, and the latest trends in the industry.
II. Types of Resistors
Resistors can be broadly categorized into three main types: fixed resistors, variable resistors, and specialty resistors. Each category encompasses various subtypes, each designed for specific applications and performance requirements.
A. Fixed Resistors
Fixed resistors are the most common type, providing a constant resistance value. They are widely used in electronic circuits for various purposes.
1. **Carbon Composition Resistors**: Made from a mixture of carbon and a binding material, these resistors are known for their high energy absorption and ability to withstand high temperatures. However, they have a relatively high tolerance and are less stable than other types.
2. **Carbon Film Resistors**: These resistors are made by depositing a thin layer of carbon on a ceramic substrate. They offer better stability and lower noise compared to carbon composition resistors, making them suitable for audio applications.
3. **Metal Film Resistors**: Constructed from a thin film of metal, these resistors provide high precision and low temperature coefficients. They are commonly used in applications requiring high accuracy, such as in measurement devices.
4. **Wirewound Resistors**: These resistors are made by winding a metal wire around a ceramic or fiberglass core. They can handle high power levels and are often used in power applications, such as in power supplies and amplifiers.
5. **Thick Film Resistors**: Made by printing a thick layer of resistive material onto a substrate, these resistors are cost-effective and suitable for surface mount technology (SMT). They are widely used in consumer electronics.
6. **Thin Film Resistors**: Similar to thick film resistors but with a thinner layer of resistive material, thin film resistors offer higher precision and stability. They are often used in high-frequency applications.
B. Variable Resistors
Variable resistors allow for adjustable resistance values, making them versatile components in electronic circuits.
1. **Potentiometers**: These are three-terminal devices that can adjust voltage levels in a circuit. They are commonly used in volume controls, tuning circuits, and other applications where variable resistance is needed.
2. **Rheostats**: A type of variable resistor, rheostats are used to control current flow in a circuit. They are often employed in applications requiring high power, such as in lighting controls and motor speed adjustments.
C. Specialty Resistors
Specialty resistors are designed for specific applications and often have unique characteristics.
1. **Precision Resistors**: These resistors have tight tolerance levels and are used in applications where accuracy is critical, such as in instrumentation and measurement devices.
2. **High-Voltage Resistors**: Designed to withstand high voltage levels, these resistors are used in applications such as power supplies and high-voltage testing equipment.
3. **High-Power Resistors**: Capable of dissipating significant amounts of power, high-power resistors are used in applications like power amplifiers and industrial equipment.
4. **Current Sensing Resistors**: These resistors are used to measure current flow in a circuit. They are often employed in power management systems and battery monitoring applications.
5. **Thermistors**: Temperature-sensitive resistors, thermistors change resistance with temperature variations. They are commonly used in temperature sensing and control applications.
6. **Varistors**: Voltage-dependent resistors, varistors protect circuits from voltage spikes by changing resistance based on the applied voltage. They are often used in surge protection devices.
7. **Photoresistors**: Also known as light-dependent resistors (LDRs), these resistors change resistance based on light exposure. They are commonly used in light-sensing applications, such as automatic lighting systems.
III. Manufacturing Processes
The manufacturing of resistors involves several key processes, from material selection to quality control.
A. Overview of the Resistor Manufacturing Process
The resistor manufacturing process typically begins with the selection of appropriate materials, followed by the fabrication of the resistive element, and finally, the assembly and testing of the finished product. Each step is crucial to ensure the performance and reliability of the resistors.
B. Materials Used in Resistor Production
1. **Conductive Materials**: The choice of conductive materials is critical in determining the resistance value and performance of the resistor. Common materials include carbon, metal films, and metal wires.
2. **Insulating Materials**: Insulating materials are used to encase the resistive element and prevent short circuits. Common insulating materials include ceramics, plastics, and glass.
C. Quality Control Measures in Resistor Manufacturing
Quality control is essential in resistor manufacturing to ensure that products meet industry standards and specifications. This includes testing for resistance values, temperature coefficients, and tolerance levels. Manufacturers often employ automated testing equipment to streamline the quality assurance process.
IV. Applications of Resistors
Resistors are used in a wide range of applications across various industries, highlighting their versatility and importance.
A. Consumer Electronics
In consumer electronics, resistors are used in devices such as televisions, smartphones, and computers to control current flow, manage voltage levels, and protect sensitive components.
B. Automotive Industry
In the automotive industry, resistors play a crucial role in electronic control systems, sensors, and lighting systems, ensuring the proper functioning of modern vehicles.
C. Industrial Equipment
Resistors are used in industrial equipment for power management, motor control, and automation systems, contributing to the efficiency and reliability of manufacturing processes.
D. Telecommunications
In telecommunications, resistors are essential for signal processing, impedance matching, and circuit protection, enabling reliable communication systems.
E. Medical Devices
In medical devices, precision resistors are used in diagnostic equipment, monitoring systems, and therapeutic devices, ensuring accurate measurements and safe operation.
V. Trends in Resistor Manufacturing
The resistor manufacturing industry is evolving, driven by technological advancements and changing market demands.
A. Technological Advancements
Innovations in materials and manufacturing techniques are leading to the development of more efficient and reliable resistors. For example, advancements in thin film technology are enabling the production of smaller, more precise resistors.
B. Demand for Miniaturization
As electronic devices become smaller and more compact, there is a growing demand for miniaturized resistors. Manufacturers are responding by developing smaller form factors and surface mount technology (SMT) resistors.
C. Environmental Considerations
With increasing awareness of environmental issues, resistor manufacturers are focusing on sustainable practices, such as using eco-friendly materials and reducing waste in the production process.
D. Custom Resistor Solutions
As industries seek tailored solutions for specific applications, there is a rising demand for custom resistor designs. Manufacturers are increasingly offering bespoke resistor solutions to meet unique performance requirements.
VI. Conclusion
Resistors are indispensable components in modern electronics, playing a vital role in controlling current flow and ensuring the proper functioning of devices across various industries. The resistor manufacturing industry encompasses a wide range of product types, from fixed and variable resistors to specialty resistors, each designed for specific applications. As technology continues to advance, the industry is evolving to meet the demands for miniaturization, precision, and sustainability. The future outlook for resistor factories is promising, with ongoing innovations and a growing emphasis on custom solutions, ensuring that resistors will remain a cornerstone of electronic design and manufacturing.
VII. References
1. Academic journals on electronics and materials science.
2. Industry reports from market research firms.
3. Manufacturer websites for product specifications and innovations.
4. Technical manuals and guides on resistor technology and applications.