What are the Manufacturing Processes of the Latest Sensitive Resistors?
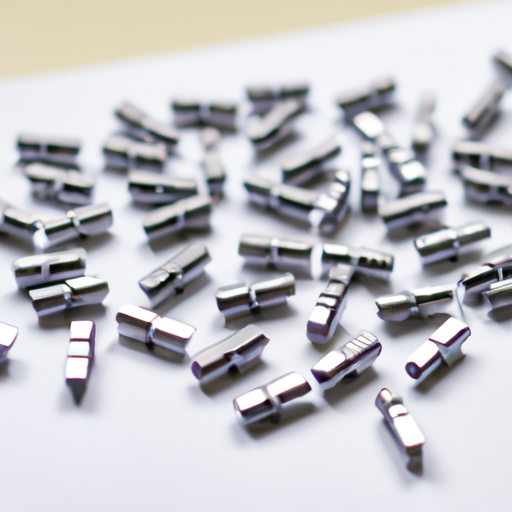
I. Introduction
Sensitive resistors are crucial components in modern electronics, playing a vital role in various applications, from temperature sensing to light detection. These resistors are designed to respond to changes in environmental conditions, making them essential for devices that require precise measurements and control. As technology advances, the manufacturing processes for these sensitive resistors have evolved, incorporating new materials and techniques to enhance performance and reliability. This blog post will explore the types of sensitive resistors, the raw materials used in their production, key manufacturing processes, innovations in the field, challenges faced, and future trends.
II. Types of Sensitive Resistors
Sensitive resistors come in various forms, each tailored for specific applications.
A. Overview of Different Types of Sensitive Resistors
1. **Thermistors**: These temperature-sensitive resistors change resistance with temperature variations. They are widely used in temperature sensing and control applications, such as in thermostats and automotive systems.
2. **Photoresistors**: Also known as light-dependent resistors (LDRs), photoresistors change resistance based on light intensity. They are commonly used in light-sensing applications, such as automatic streetlights and camera exposure controls.
3. **Strain Gauges**: These resistors measure deformation or strain in materials. They are essential in structural health monitoring, load cells, and various industrial applications.
4. **Other Specialized Resistors**: This category includes piezoresistive sensors, gas sensors, and humidity sensors, each designed for specific environmental measurements.
B. Applications of Each Type in Various Industries
Sensitive resistors find applications across multiple industries, including automotive, aerospace, healthcare, and consumer electronics. For instance, thermistors are crucial in medical devices for monitoring body temperature, while photoresistors are integral to smart lighting systems in urban infrastructure.
III. Raw Materials Used in Manufacturing
The performance of sensitive resistors largely depends on the quality of raw materials used in their production.
A. Conductive Materials
1. **Metal Oxides**: Commonly used in thermistors, metal oxides like tin oxide and nickel oxide exhibit significant changes in resistance with temperature variations.
2. **Carbon-Based Materials**: Carbon nanotubes and graphene are increasingly being explored for their excellent conductivity and sensitivity, particularly in advanced sensor applications.
B. Insulating Materials
1. **Ceramics**: These materials provide excellent thermal stability and insulation, making them ideal for high-temperature applications.
2. **Polymers**: Flexible and lightweight, polymers are often used in applications requiring conformability and durability.
C. Substrates and Packaging Materials
The choice of substrate and packaging materials is critical for protecting sensitive resistors from environmental factors and ensuring reliable performance. Common materials include glass, silicon, and various plastics.
IV. Key Manufacturing Processes
The manufacturing of sensitive resistors involves several key processes, each contributing to the final product's performance and reliability.
A. Material Preparation
1. **Sourcing and Quality Control of Raw Materials**: Ensuring high-quality raw materials is essential for producing reliable sensitive resistors. Manufacturers often establish strict quality control measures to verify the purity and consistency of materials.
2. **Pre-Processing Techniques**: Techniques such as grinding and mixing are employed to prepare raw materials for fabrication. This step ensures uniformity in the material properties, which is crucial for consistent performance.
B. Fabrication Techniques
1. **Screen Printing**: This technique is commonly used for applying conductive inks onto substrates. It allows for precise control over the thickness and pattern of the resistive layer.
2. **Thin-Film Deposition**: In this process, thin layers of conductive materials are deposited onto substrates using methods like sputtering or chemical vapor deposition. This technique is essential for creating high-precision resistors.
3. **Thick-Film Technology**: Thick-film resistors are made by printing a paste of conductive material onto a substrate and then firing it at high temperatures. This method is widely used for producing robust and reliable resistors.
4. **Laser Cutting and Etching**: These techniques are employed to create intricate patterns and shapes in resistive materials, allowing for the production of complex resistor designs.
C. Assembly Processes
1. **Mounting and Soldering**: After fabrication, sensitive resistors are mounted onto circuit boards and soldered to ensure electrical connections. This step is critical for the functionality of the final product.
2. **Encapsulation and Packaging**: To protect sensitive resistors from environmental factors, they are often encapsulated in protective materials. This step enhances durability and reliability, especially in harsh conditions.
D. Testing and Quality Assurance
1. **Electrical Testing**: Each resistor undergoes rigorous electrical testing to ensure it meets specified resistance values and performance criteria.
2. **Environmental Testing**: Resistors are subjected to various environmental conditions, such as temperature and humidity extremes, to assess their reliability and performance under real-world conditions.
3. **Reliability Testing**: Long-term reliability tests are conducted to evaluate the lifespan and durability of sensitive resistors, ensuring they can withstand prolonged use.
V. Innovations in Manufacturing Processes
The field of sensitive resistor manufacturing is continuously evolving, driven by advancements in materials science and technology.
A. Advances in Materials Science
1. **Development of New Conductive Materials**: Researchers are exploring novel conductive materials, such as nanomaterials and composites, to enhance the sensitivity and performance of resistors.
2. **Nanotechnology Applications**: The integration of nanotechnology in resistor manufacturing allows for the creation of smaller, more sensitive devices with improved performance characteristics.
B. Automation and Industry 4.0
1. **Smart Manufacturing Techniques**: The adoption of smart manufacturing practices, including IoT and real-time monitoring, enhances production efficiency and quality control.
2. **Use of AI and Machine Learning in Production**: AI algorithms are increasingly being used to optimize manufacturing processes, predict failures, and improve product design.
C. Sustainability in Manufacturing
1. **Eco-Friendly Materials and Processes**: Manufacturers are increasingly focusing on sustainable practices, such as using biodegradable materials and reducing energy consumption during production.
2. **Waste Reduction Strategies**: Implementing strategies to minimize waste during manufacturing not only benefits the environment but also reduces production costs.
VI. Challenges in Manufacturing Sensitive Resistors
Despite advancements, the manufacturing of sensitive resistors faces several challenges.
A. Precision and Accuracy in Production
Achieving high precision and accuracy in the production of sensitive resistors is critical, as even minor deviations can significantly impact performance.
B. Cost Management and Economic Factors
Manufacturers must balance the costs of high-quality materials and advanced manufacturing techniques with the need to remain competitive in the market.
C. Meeting Industry Standards and Regulations
Compliance with industry standards and regulations is essential for ensuring product safety and reliability. Manufacturers must stay updated on changing regulations and adapt their processes accordingly.
VII. Future Trends in Sensitive Resistor Manufacturing
The future of sensitive resistor manufacturing is poised for exciting developments.
A. Emerging Technologies and Their Impact
Technologies such as 3D printing and advanced nanofabrication techniques are expected to revolutionize the production of sensitive resistors, enabling the creation of more complex and efficient designs.
B. Predictions for the Evolution of Sensitive Resistors
As the demand for smart devices and IoT applications grows, sensitive resistors will likely evolve to meet the needs of increasingly sophisticated technologies.
C. Potential New Applications in Various Fields
The versatility of sensitive resistors opens up possibilities for new applications in fields such as healthcare, environmental monitoring, and smart cities, driving further innovation in manufacturing processes.
VIII. Conclusion
Sensitive resistors are integral to modern electronics, enabling precise measurements and control in various applications. The manufacturing processes for these components have evolved significantly, incorporating advanced materials and techniques to enhance performance and reliability. As technology continues to advance, the future of sensitive resistor manufacturing holds great promise, with emerging technologies and innovative practices paving the way for new applications and improved products.
IX. References
1. Academic journals on materials science and electronics manufacturing.
2. Industry reports on trends in sensor technology.
3. Books and articles discussing the principles of resistor design and manufacturing processes.
This comprehensive overview of the manufacturing processes of sensitive resistors highlights their importance in modern technology and the continuous innovations shaping their future.
What are the Manufacturing Processes of the Latest Sensitive Resistors?
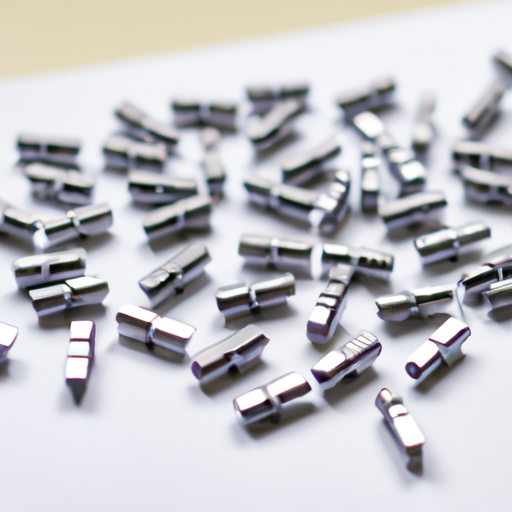
I. Introduction
Sensitive resistors are crucial components in modern electronics, playing a vital role in various applications, from temperature sensing to light detection. These resistors are designed to respond to changes in environmental conditions, making them essential for devices that require precise measurements and control. As technology advances, the manufacturing processes for these sensitive resistors have evolved, incorporating new materials and techniques to enhance performance and reliability. This blog post will explore the types of sensitive resistors, the raw materials used in their production, key manufacturing processes, innovations in the field, challenges faced, and future trends.
II. Types of Sensitive Resistors
Sensitive resistors come in various forms, each tailored for specific applications.
A. Overview of Different Types of Sensitive Resistors
1. **Thermistors**: These temperature-sensitive resistors change resistance with temperature variations. They are widely used in temperature sensing and control applications, such as in thermostats and automotive systems.
2. **Photoresistors**: Also known as light-dependent resistors (LDRs), photoresistors change resistance based on light intensity. They are commonly used in light-sensing applications, such as automatic streetlights and camera exposure controls.
3. **Strain Gauges**: These resistors measure deformation or strain in materials. They are essential in structural health monitoring, load cells, and various industrial applications.
4. **Other Specialized Resistors**: This category includes piezoresistive sensors, gas sensors, and humidity sensors, each designed for specific environmental measurements.
B. Applications of Each Type in Various Industries
Sensitive resistors find applications across multiple industries, including automotive, aerospace, healthcare, and consumer electronics. For instance, thermistors are crucial in medical devices for monitoring body temperature, while photoresistors are integral to smart lighting systems in urban infrastructure.
III. Raw Materials Used in Manufacturing
The performance of sensitive resistors largely depends on the quality of raw materials used in their production.
A. Conductive Materials
1. **Metal Oxides**: Commonly used in thermistors, metal oxides like tin oxide and nickel oxide exhibit significant changes in resistance with temperature variations.
2. **Carbon-Based Materials**: Carbon nanotubes and graphene are increasingly being explored for their excellent conductivity and sensitivity, particularly in advanced sensor applications.
B. Insulating Materials
1. **Ceramics**: These materials provide excellent thermal stability and insulation, making them ideal for high-temperature applications.
2. **Polymers**: Flexible and lightweight, polymers are often used in applications requiring conformability and durability.
C. Substrates and Packaging Materials
The choice of substrate and packaging materials is critical for protecting sensitive resistors from environmental factors and ensuring reliable performance. Common materials include glass, silicon, and various plastics.
IV. Key Manufacturing Processes
The manufacturing of sensitive resistors involves several key processes, each contributing to the final product's performance and reliability.
A. Material Preparation
1. **Sourcing and Quality Control of Raw Materials**: Ensuring high-quality raw materials is essential for producing reliable sensitive resistors. Manufacturers often establish strict quality control measures to verify the purity and consistency of materials.
2. **Pre-Processing Techniques**: Techniques such as grinding and mixing are employed to prepare raw materials for fabrication. This step ensures uniformity in the material properties, which is crucial for consistent performance.
B. Fabrication Techniques
1. **Screen Printing**: This technique is commonly used for applying conductive inks onto substrates. It allows for precise control over the thickness and pattern of the resistive layer.
2. **Thin-Film Deposition**: In this process, thin layers of conductive materials are deposited onto substrates using methods like sputtering or chemical vapor deposition. This technique is essential for creating high-precision resistors.
3. **Thick-Film Technology**: Thick-film resistors are made by printing a paste of conductive material onto a substrate and then firing it at high temperatures. This method is widely used for producing robust and reliable resistors.
4. **Laser Cutting and Etching**: These techniques are employed to create intricate patterns and shapes in resistive materials, allowing for the production of complex resistor designs.
C. Assembly Processes
1. **Mounting and Soldering**: After fabrication, sensitive resistors are mounted onto circuit boards and soldered to ensure electrical connections. This step is critical for the functionality of the final product.
2. **Encapsulation and Packaging**: To protect sensitive resistors from environmental factors, they are often encapsulated in protective materials. This step enhances durability and reliability, especially in harsh conditions.
D. Testing and Quality Assurance
1. **Electrical Testing**: Each resistor undergoes rigorous electrical testing to ensure it meets specified resistance values and performance criteria.
2. **Environmental Testing**: Resistors are subjected to various environmental conditions, such as temperature and humidity extremes, to assess their reliability and performance under real-world conditions.
3. **Reliability Testing**: Long-term reliability tests are conducted to evaluate the lifespan and durability of sensitive resistors, ensuring they can withstand prolonged use.
V. Innovations in Manufacturing Processes
The field of sensitive resistor manufacturing is continuously evolving, driven by advancements in materials science and technology.
A. Advances in Materials Science
1. **Development of New Conductive Materials**: Researchers are exploring novel conductive materials, such as nanomaterials and composites, to enhance the sensitivity and performance of resistors.
2. **Nanotechnology Applications**: The integration of nanotechnology in resistor manufacturing allows for the creation of smaller, more sensitive devices with improved performance characteristics.
B. Automation and Industry 4.0
1. **Smart Manufacturing Techniques**: The adoption of smart manufacturing practices, including IoT and real-time monitoring, enhances production efficiency and quality control.
2. **Use of AI and Machine Learning in Production**: AI algorithms are increasingly being used to optimize manufacturing processes, predict failures, and improve product design.
C. Sustainability in Manufacturing
1. **Eco-Friendly Materials and Processes**: Manufacturers are increasingly focusing on sustainable practices, such as using biodegradable materials and reducing energy consumption during production.
2. **Waste Reduction Strategies**: Implementing strategies to minimize waste during manufacturing not only benefits the environment but also reduces production costs.
VI. Challenges in Manufacturing Sensitive Resistors
Despite advancements, the manufacturing of sensitive resistors faces several challenges.
A. Precision and Accuracy in Production
Achieving high precision and accuracy in the production of sensitive resistors is critical, as even minor deviations can significantly impact performance.
B. Cost Management and Economic Factors
Manufacturers must balance the costs of high-quality materials and advanced manufacturing techniques with the need to remain competitive in the market.
C. Meeting Industry Standards and Regulations
Compliance with industry standards and regulations is essential for ensuring product safety and reliability. Manufacturers must stay updated on changing regulations and adapt their processes accordingly.
VII. Future Trends in Sensitive Resistor Manufacturing
The future of sensitive resistor manufacturing is poised for exciting developments.
A. Emerging Technologies and Their Impact
Technologies such as 3D printing and advanced nanofabrication techniques are expected to revolutionize the production of sensitive resistors, enabling the creation of more complex and efficient designs.
B. Predictions for the Evolution of Sensitive Resistors
As the demand for smart devices and IoT applications grows, sensitive resistors will likely evolve to meet the needs of increasingly sophisticated technologies.
C. Potential New Applications in Various Fields
The versatility of sensitive resistors opens up possibilities for new applications in fields such as healthcare, environmental monitoring, and smart cities, driving further innovation in manufacturing processes.
VIII. Conclusion
Sensitive resistors are integral to modern electronics, enabling precise measurements and control in various applications. The manufacturing processes for these components have evolved significantly, incorporating advanced materials and techniques to enhance performance and reliability. As technology continues to advance, the future of sensitive resistor manufacturing holds great promise, with emerging technologies and innovative practices paving the way for new applications and improved products.
IX. References
1. Academic journals on materials science and electronics manufacturing.
2. Industry reports on trends in sensor technology.
3. Books and articles discussing the principles of resistor design and manufacturing processes.
This comprehensive overview of the manufacturing processes of sensitive resistors highlights their importance in modern technology and the continuous innovations shaping their future.