Common Production Processes for Metal Film Resistors
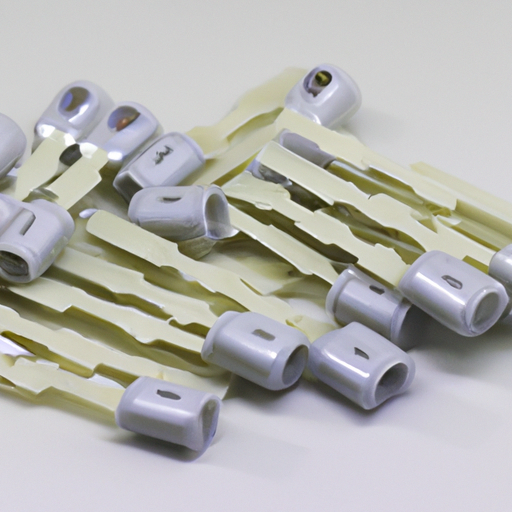
I. Introduction
A. Definition of Metal Film Resistors
Metal film resistors are passive electronic components that provide resistance in electrical circuits. They are made by depositing a thin layer of metal onto a substrate, which is then patterned to create a specific resistance value. Known for their precision and stability, metal film resistors are widely used in various electronic applications, from consumer electronics to industrial equipment.
B. Importance of Metal Film Resistors in Electronics
The significance of metal film resistors in electronics cannot be overstated. They offer several advantages over other types of resistors, such as carbon film or wire-wound resistors. Metal film resistors exhibit low noise, high accuracy, and excellent temperature stability, making them ideal for applications that require precise resistance values. Their reliability and performance have made them a preferred choice in high-end audio equipment, medical devices, and precision measurement instruments.
C. Overview of the Production Process
The production of metal film resistors involves several key processes, from selecting raw materials to final testing and quality control. Understanding these processes is essential for manufacturers aiming to produce high-quality resistors that meet industry standards.
II. Raw Materials
A. Types of Metals Used
1. Nickel-Chromium Alloys
The primary material used in metal film resistors is nickel-chromium alloy, known for its excellent resistive properties. This alloy provides a stable resistance value and is less susceptible to temperature variations, making it ideal for precision applications.
2. Other Conductive Materials
In addition to nickel-chromium, other conductive materials such as tantalum, platinum, and various metal oxides may also be used, depending on the specific requirements of the resistor. These materials can enhance the performance characteristics of the resistors, such as their temperature coefficient and stability.
B. Substrate Materials
1. Ceramic Substrates
Ceramic substrates are commonly used in the production of metal film resistors due to their excellent thermal stability and electrical insulation properties. They provide a robust base for the metal film and help maintain the resistor's performance under varying environmental conditions.
2. Glass and Other Materials
In some cases, glass or other materials may be used as substrates. These materials can offer unique properties, such as improved thermal conductivity or specific dielectric characteristics, which can be beneficial for certain applications.
C. Additional Components
1. Protective Coatings
To enhance durability and protect against environmental factors, metal film resistors are often coated with protective materials. These coatings can prevent moisture ingress, chemical exposure, and mechanical damage.
2. Adhesives and Binders
Adhesives and binders are used to secure the metal film to the substrate and ensure the integrity of the resistor during operation. The choice of adhesive can impact the thermal and electrical performance of the final product.
III. Design and Specifications
A. Resistance Value Determination
The resistance value of a metal film resistor is determined during the design phase. This involves calculating the desired resistance based on the application requirements and the properties of the materials used. The thickness and width of the metal film play a crucial role in achieving the specified resistance.
B. Tolerance and Temperature Coefficient
Tolerance refers to the allowable deviation from the nominal resistance value, while the temperature coefficient indicates how much the resistance changes with temperature. Both parameters are critical in ensuring that the resistor performs reliably under varying conditions.
C. Size and Form Factor Considerations
The physical dimensions of the resistor are also important. Manufacturers must consider the size and form factor to ensure compatibility with circuit designs and to meet specific application requirements.
IV. Production Processes
A. Thin Film Deposition
1. Physical Vapor Deposition (PVD)
One of the primary methods for depositing the metal film is Physical Vapor Deposition (PVD). In this process, the metal is vaporized in a vacuum chamber and then condensed onto the substrate, forming a thin film. PVD allows for precise control over the thickness and uniformity of the metal layer.
2. Chemical Vapor Deposition (CVD)
Chemical Vapor Deposition (CVD) is another technique used to create the metal film. In this process, gaseous precursors react on the substrate surface to form a solid metal layer. CVD can produce high-quality films with excellent adhesion and uniformity.
B. Patterning
1. Photolithography
Once the metal film is deposited, it must be patterned to create the desired resistance value. Photolithography is a common technique used for this purpose. A photoresist material is applied to the metal film, exposed to light through a mask, and then developed to create a pattern that defines the resistor's geometry.
2. Laser Etching
Laser etching is an alternative method for patterning the metal film. This technique uses a focused laser beam to remove specific areas of the metal layer, allowing for precise control over the resistor's dimensions.
C. Trimming
1. Laser Trimming
After patterning, the resistance value may need to be fine-tuned. Laser trimming is a precise method used to adjust the resistance by selectively removing material from the metal film. This process allows manufacturers to achieve the desired resistance value with high accuracy.
2. Mechanical Trimming
Mechanical trimming is another method used to adjust resistance values. This process involves physically cutting or grinding the metal film to achieve the desired resistance. While less precise than laser trimming, it can be effective for certain applications.
D. Passivation
1. Application of Protective Coatings
To protect the resistor from environmental factors, a passivation layer is applied. This layer can be made from various materials, including epoxy or silicone, and serves to shield the resistor from moisture, dust, and chemicals.
2. Curing Processes
After applying the protective coating, curing processes are employed to ensure that the coating adheres properly and achieves its desired properties. This may involve heating or exposing the resistors to specific environmental conditions.
V. Testing and Quality Control
A. Electrical Testing
1. Resistance Measurement
Once the resistors are produced, they undergo rigorous electrical testing to verify their resistance values. Automated testing equipment measures the resistance and ensures that it falls within the specified tolerance range.
2. Temperature Coefficient Testing
Temperature coefficient testing is conducted to assess how the resistance changes with temperature. This testing is crucial for applications where temperature variations are expected.
B. Mechanical Testing
1. Stress Testing
Mechanical testing involves subjecting the resistors to various stress conditions to evaluate their durability. This may include thermal cycling, vibration testing, and mechanical stress tests to ensure that the resistors can withstand real-world conditions.
2. Environmental Testing
Environmental testing assesses the performance of resistors under different environmental conditions, such as humidity, temperature extremes, and exposure to chemicals. This testing helps ensure that the resistors will perform reliably in their intended applications.
C. Final Inspection and Packaging
After testing, each batch of resistors undergoes a final inspection to ensure that they meet quality standards. Once approved, the resistors are packaged for shipment, ensuring that they are protected during transport.
VI. Environmental Considerations
A. Waste Management in Production
The production of metal film resistors generates waste materials, including metal scraps and chemical byproducts. Manufacturers must implement effective waste management practices to minimize environmental impact and comply with regulations.
B. Compliance with Environmental Regulations
Adhering to environmental regulations is essential for manufacturers. This includes compliance with standards related to hazardous materials, emissions, and waste disposal.
C. Sustainable Practices in Manufacturing
Many manufacturers are adopting sustainable practices in their production processes. This includes using eco-friendly materials, reducing energy consumption, and implementing recycling programs to minimize waste.
VII. Conclusion
A. Summary of Key Production Processes
The production of metal film resistors involves a series of intricate processes, from selecting raw materials to final testing and quality control. Each step is crucial in ensuring that the resistors meet the high standards required for modern electronic applications.
B. Future Trends in Metal Film Resistor Production
As technology advances, the demand for more precise and reliable electronic components continues to grow. Future trends in metal film resistor production may include the development of new materials, improved manufacturing techniques, and enhanced testing methods to meet the evolving needs of the industry.
C. Importance of Quality in Electronic Components
Ultimately, the quality of metal film resistors plays a vital role in the performance and reliability of electronic devices. Manufacturers must prioritize quality at every stage of production to ensure that their products meet the high standards expected by consumers and industry professionals alike.
VIII. References
A. Academic Journals
- Journal of Electronic Materials
- IEEE Transactions on Components, Packaging and Manufacturing Technology
B. Industry Standards and Guidelines
- International Electrotechnical Commission (IEC) Standards
- American National Standards Institute (ANSI) Guidelines
C. Manufacturer Specifications and White Papers
- Manufacturer datasheets and technical documents
- White papers on advancements in resistor technology
---
This blog post provides a comprehensive overview of the common production processes for metal film resistors, highlighting the importance of each step in ensuring high-quality electronic components.
Common Production Processes for Metal Film Resistors
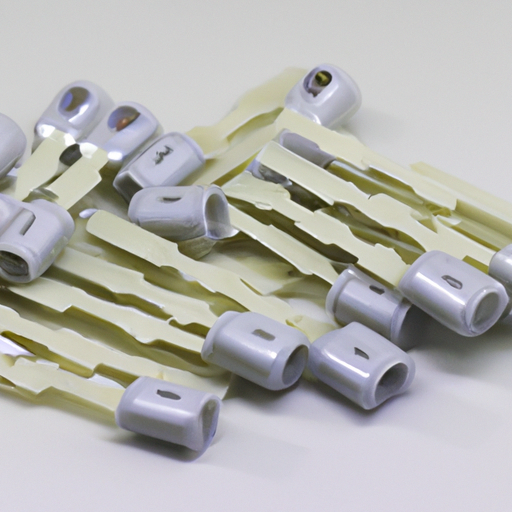
I. Introduction
A. Definition of Metal Film Resistors
Metal film resistors are passive electronic components that provide resistance in electrical circuits. They are made by depositing a thin layer of metal onto a substrate, which is then patterned to create a specific resistance value. Known for their precision and stability, metal film resistors are widely used in various electronic applications, from consumer electronics to industrial equipment.
B. Importance of Metal Film Resistors in Electronics
The significance of metal film resistors in electronics cannot be overstated. They offer several advantages over other types of resistors, such as carbon film or wire-wound resistors. Metal film resistors exhibit low noise, high accuracy, and excellent temperature stability, making them ideal for applications that require precise resistance values. Their reliability and performance have made them a preferred choice in high-end audio equipment, medical devices, and precision measurement instruments.
C. Overview of the Production Process
The production of metal film resistors involves several key processes, from selecting raw materials to final testing and quality control. Understanding these processes is essential for manufacturers aiming to produce high-quality resistors that meet industry standards.
II. Raw Materials
A. Types of Metals Used
1. Nickel-Chromium Alloys
The primary material used in metal film resistors is nickel-chromium alloy, known for its excellent resistive properties. This alloy provides a stable resistance value and is less susceptible to temperature variations, making it ideal for precision applications.
2. Other Conductive Materials
In addition to nickel-chromium, other conductive materials such as tantalum, platinum, and various metal oxides may also be used, depending on the specific requirements of the resistor. These materials can enhance the performance characteristics of the resistors, such as their temperature coefficient and stability.
B. Substrate Materials
1. Ceramic Substrates
Ceramic substrates are commonly used in the production of metal film resistors due to their excellent thermal stability and electrical insulation properties. They provide a robust base for the metal film and help maintain the resistor's performance under varying environmental conditions.
2. Glass and Other Materials
In some cases, glass or other materials may be used as substrates. These materials can offer unique properties, such as improved thermal conductivity or specific dielectric characteristics, which can be beneficial for certain applications.
C. Additional Components
1. Protective Coatings
To enhance durability and protect against environmental factors, metal film resistors are often coated with protective materials. These coatings can prevent moisture ingress, chemical exposure, and mechanical damage.
2. Adhesives and Binders
Adhesives and binders are used to secure the metal film to the substrate and ensure the integrity of the resistor during operation. The choice of adhesive can impact the thermal and electrical performance of the final product.
III. Design and Specifications
A. Resistance Value Determination
The resistance value of a metal film resistor is determined during the design phase. This involves calculating the desired resistance based on the application requirements and the properties of the materials used. The thickness and width of the metal film play a crucial role in achieving the specified resistance.
B. Tolerance and Temperature Coefficient
Tolerance refers to the allowable deviation from the nominal resistance value, while the temperature coefficient indicates how much the resistance changes with temperature. Both parameters are critical in ensuring that the resistor performs reliably under varying conditions.
C. Size and Form Factor Considerations
The physical dimensions of the resistor are also important. Manufacturers must consider the size and form factor to ensure compatibility with circuit designs and to meet specific application requirements.
IV. Production Processes
A. Thin Film Deposition
1. Physical Vapor Deposition (PVD)
One of the primary methods for depositing the metal film is Physical Vapor Deposition (PVD). In this process, the metal is vaporized in a vacuum chamber and then condensed onto the substrate, forming a thin film. PVD allows for precise control over the thickness and uniformity of the metal layer.
2. Chemical Vapor Deposition (CVD)
Chemical Vapor Deposition (CVD) is another technique used to create the metal film. In this process, gaseous precursors react on the substrate surface to form a solid metal layer. CVD can produce high-quality films with excellent adhesion and uniformity.
B. Patterning
1. Photolithography
Once the metal film is deposited, it must be patterned to create the desired resistance value. Photolithography is a common technique used for this purpose. A photoresist material is applied to the metal film, exposed to light through a mask, and then developed to create a pattern that defines the resistor's geometry.
2. Laser Etching
Laser etching is an alternative method for patterning the metal film. This technique uses a focused laser beam to remove specific areas of the metal layer, allowing for precise control over the resistor's dimensions.
C. Trimming
1. Laser Trimming
After patterning, the resistance value may need to be fine-tuned. Laser trimming is a precise method used to adjust the resistance by selectively removing material from the metal film. This process allows manufacturers to achieve the desired resistance value with high accuracy.
2. Mechanical Trimming
Mechanical trimming is another method used to adjust resistance values. This process involves physically cutting or grinding the metal film to achieve the desired resistance. While less precise than laser trimming, it can be effective for certain applications.
D. Passivation
1. Application of Protective Coatings
To protect the resistor from environmental factors, a passivation layer is applied. This layer can be made from various materials, including epoxy or silicone, and serves to shield the resistor from moisture, dust, and chemicals.
2. Curing Processes
After applying the protective coating, curing processes are employed to ensure that the coating adheres properly and achieves its desired properties. This may involve heating or exposing the resistors to specific environmental conditions.
V. Testing and Quality Control
A. Electrical Testing
1. Resistance Measurement
Once the resistors are produced, they undergo rigorous electrical testing to verify their resistance values. Automated testing equipment measures the resistance and ensures that it falls within the specified tolerance range.
2. Temperature Coefficient Testing
Temperature coefficient testing is conducted to assess how the resistance changes with temperature. This testing is crucial for applications where temperature variations are expected.
B. Mechanical Testing
1. Stress Testing
Mechanical testing involves subjecting the resistors to various stress conditions to evaluate their durability. This may include thermal cycling, vibration testing, and mechanical stress tests to ensure that the resistors can withstand real-world conditions.
2. Environmental Testing
Environmental testing assesses the performance of resistors under different environmental conditions, such as humidity, temperature extremes, and exposure to chemicals. This testing helps ensure that the resistors will perform reliably in their intended applications.
C. Final Inspection and Packaging
After testing, each batch of resistors undergoes a final inspection to ensure that they meet quality standards. Once approved, the resistors are packaged for shipment, ensuring that they are protected during transport.
VI. Environmental Considerations
A. Waste Management in Production
The production of metal film resistors generates waste materials, including metal scraps and chemical byproducts. Manufacturers must implement effective waste management practices to minimize environmental impact and comply with regulations.
B. Compliance with Environmental Regulations
Adhering to environmental regulations is essential for manufacturers. This includes compliance with standards related to hazardous materials, emissions, and waste disposal.
C. Sustainable Practices in Manufacturing
Many manufacturers are adopting sustainable practices in their production processes. This includes using eco-friendly materials, reducing energy consumption, and implementing recycling programs to minimize waste.
VII. Conclusion
A. Summary of Key Production Processes
The production of metal film resistors involves a series of intricate processes, from selecting raw materials to final testing and quality control. Each step is crucial in ensuring that the resistors meet the high standards required for modern electronic applications.
B. Future Trends in Metal Film Resistor Production
As technology advances, the demand for more precise and reliable electronic components continues to grow. Future trends in metal film resistor production may include the development of new materials, improved manufacturing techniques, and enhanced testing methods to meet the evolving needs of the industry.
C. Importance of Quality in Electronic Components
Ultimately, the quality of metal film resistors plays a vital role in the performance and reliability of electronic devices. Manufacturers must prioritize quality at every stage of production to ensure that their products meet the high standards expected by consumers and industry professionals alike.
VIII. References
A. Academic Journals
- Journal of Electronic Materials
- IEEE Transactions on Components, Packaging and Manufacturing Technology
B. Industry Standards and Guidelines
- International Electrotechnical Commission (IEC) Standards
- American National Standards Institute (ANSI) Guidelines
C. Manufacturer Specifications and White Papers
- Manufacturer datasheets and technical documents
- White papers on advancements in resistor technology
---
This blog post provides a comprehensive overview of the common production processes for metal film resistors, highlighting the importance of each step in ensuring high-quality electronic components.