What is the Mainstream Chip Resistor Production Process?
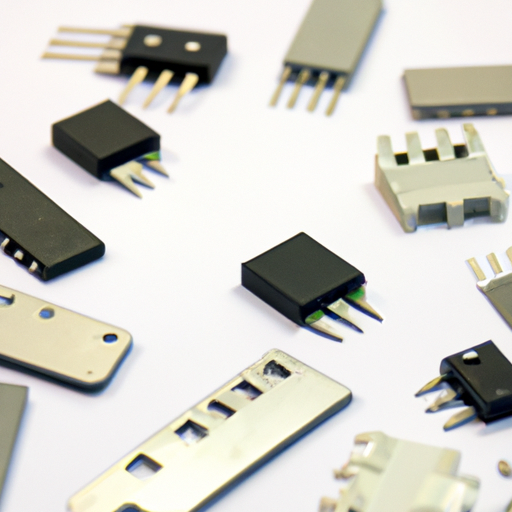
I. Introduction
Chip resistors, also known as surface mount resistors, are essential components in modern electronic circuits. These tiny devices play a crucial role in controlling the flow of electric current, ensuring that circuits function correctly and efficiently. As the demand for smaller, more efficient electronic devices continues to rise, understanding the production process of chip resistors becomes increasingly important. This blog post will provide an in-depth look at the mainstream chip resistor production process, from raw materials to innovations shaping the future of the industry.
II. Raw Materials
The production of chip resistors begins with the selection of high-quality raw materials. The primary materials used in chip resistors include ceramic substrates, metal films, and conductive pastes.
A. Types of Materials Used in Chip Resistors
1. **Ceramic Substrates**: Ceramic materials are favored for their excellent thermal stability and electrical insulation properties. They provide a robust base for the resistive elements and help maintain the integrity of the resistor under varying environmental conditions.
2. **Metal Films**: The resistive element in chip resistors is typically made from metal films, such as nickel-chromium or tantalum nitride. These materials are chosen for their precise resistance values and stability over time.
3. **Conductive Pastes**: Conductive pastes are used to create the electrical connections on the chip resistor. These pastes often contain a mixture of metal powders and binders, allowing for effective adhesion to the ceramic substrate.
B. Quality Control of Raw Materials
Quality control is critical in the production of chip resistors. Manufacturers must ensure that all raw materials meet stringent specifications to guarantee the performance and reliability of the final product. This involves rigorous testing and inspection of materials before they enter the production line.
C. Sourcing and Supply Chain Considerations
Sourcing high-quality raw materials is essential for maintaining production efficiency and product quality. Manufacturers often establish long-term relationships with suppliers to ensure a consistent supply of materials. Additionally, supply chain considerations, such as logistics and inventory management, play a vital role in the overall production process.
III. Design and Specifications
Before manufacturing can begin, it is essential to understand the design and specifications of chip resistors.
A. Understanding Resistor Specifications
1. **Resistance Value**: The resistance value is a critical specification that determines how much current will flow through the resistor. It is measured in ohms and can vary widely depending on the application.
2. **Tolerance**: Tolerance indicates the allowable deviation from the specified resistance value. It is typically expressed as a percentage and is crucial for applications requiring precise current control.
3. **Temperature Coefficient**: This specification describes how the resistance value changes with temperature. A low temperature coefficient is desirable for applications where temperature fluctuations are expected.
B. Design Considerations for Chip Resistors
1. **Size and Form Factor**: Chip resistors come in various sizes, and the choice of form factor depends on the specific application. Smaller resistors are often preferred for compact devices, while larger ones may be used in high-power applications.
2. **Power Rating**: The power rating indicates the maximum amount of power the resistor can dissipate without overheating. This specification is crucial for ensuring the reliability and longevity of the resistor.
C. Simulation and Modeling Techniques
Before moving to production, manufacturers often use simulation and modeling techniques to predict the performance of chip resistors under various conditions. This helps in optimizing the design and ensuring that the final product meets all specifications.
IV. Manufacturing Process
The manufacturing process of chip resistors involves several stages, each critical to producing a high-quality product.
A. Overview of the Production Stages
The production process can be broken down into several key stages, including substrate preparation, deposition of resistive material, sintering and curing, trimming and adjusting resistance values, application of protective coatings, and final inspection and testing.
B. Step-by-Step Breakdown of the Manufacturing Process
1. **Substrate Preparation**:
- **Cleaning and Surface Treatment**: The ceramic substrates undergo thorough cleaning to remove any contaminants that could affect adhesion and performance. Surface treatments may also be applied to enhance bonding.
- **Cutting and Shaping**: The substrates are cut and shaped into the desired dimensions, ensuring consistency across all units.
2. **Deposition of Resistive Material**:
- **Screen Printing**: A common method for applying the resistive material involves screen printing, where a stencil is used to deposit the metal film onto the substrate.
- **Thin-Film Deposition**: In some cases, thin-film deposition techniques, such as sputtering or evaporation, are used to create a uniform layer of resistive material.
3. **Sintering and Curing**:
- **Temperature Control**: The substrates are subjected to high temperatures in a controlled environment to sinter the resistive material, enhancing its electrical properties.
- **Time Management**: The duration of the sintering process is carefully monitored to ensure optimal results.
4. **Trimming and Adjusting Resistance Values**:
- **Laser Trimming**: This precise method involves using a laser to remove material from the resistive layer, allowing for fine-tuning of the resistance value.
- **Mechanical Trimming**: In some cases, mechanical methods may be employed to achieve the desired resistance.
5. **Application of Protective Coatings**:
- **Types of Coatings**: Various protective coatings, such as epoxy or silicone, are applied to enhance durability and protect against environmental factors.
- **Importance of Coatings for Durability**: These coatings are essential for ensuring the longevity of chip resistors, especially in harsh operating conditions.
6. **Final Inspection and Testing**:
- **Electrical Testing**: Each resistor undergoes rigorous electrical testing to verify its performance against specified parameters.
- **Visual Inspection**: A thorough visual inspection is conducted to identify any defects or inconsistencies in the manufacturing process.
V. Quality Control and Assurance
Quality control is a cornerstone of chip resistor production. Manufacturers implement strict testing methods and adhere to industry standards to ensure the reliability of their products.
A. Importance of Quality Control in Chip Resistor Production
Quality control helps prevent defects and ensures that each resistor meets the required specifications. This is particularly important in applications where failure could lead to significant consequences.
B. Testing Methods and Standards
1. **Reliability Testing**: Resistors are subjected to various stress tests to evaluate their performance under extreme conditions, such as high temperatures and humidity.
2. **Environmental Testing**: Environmental tests assess how resistors perform in different environmental conditions, ensuring they can withstand real-world applications.
C. Certification and Compliance with Industry Standards
Manufacturers often seek certification from recognized industry bodies to demonstrate compliance with established standards. This not only enhances credibility but also assures customers of the quality and reliability of the products.
VI. Packaging and Distribution
Once the chip resistors have passed all quality checks, they are prepared for packaging and distribution.
A. Packaging Methods for Chip Resistors
1. **Tape and Reel Packaging**: This method is commonly used for surface mount devices, allowing for easy handling and automated assembly in manufacturing processes.
2. **Bulk Packaging**: For certain applications, resistors may be packaged in bulk, providing flexibility for manufacturers who prefer to handle components individually.
B. Logistics and Distribution Channels
Efficient logistics and distribution channels are essential for ensuring that chip resistors reach customers in a timely manner. Manufacturers often work with logistics partners to optimize shipping and delivery processes.
C. Considerations for Global Markets
As the demand for chip resistors grows globally, manufacturers must consider various factors, such as regulatory compliance and market preferences, to successfully navigate international markets.
VII. Innovations and Future Trends
The chip resistor industry is continually evolving, driven by advancements in technology and changing market demands.
A. Advances in Chip Resistor Technology
1. **Miniaturization**: As electronic devices become smaller, the demand for miniaturized chip resistors has increased. Manufacturers are developing new techniques to produce smaller, more efficient resistors without compromising performance.
2. **Enhanced Performance Characteristics**: Innovations in materials and manufacturing processes are leading to chip resistors with improved performance characteristics, such as higher power ratings and better thermal stability.
B. Impact of Emerging Technologies
1. **IoT and Smart Devices**: The rise of the Internet of Things (IoT) and smart devices is driving demand for chip resistors that can support advanced functionalities while maintaining compact sizes.
2. **Automotive Applications**: The automotive industry is increasingly relying on chip resistors for various applications, including electric vehicles and advanced driver-assistance systems (ADAS).
C. Sustainability and Eco-Friendly Practices in Production
As environmental concerns grow, manufacturers are exploring sustainable practices in chip resistor production. This includes using eco-friendly materials and reducing waste throughout the manufacturing process.
VIII. Conclusion
In summary, the production process of chip resistors is a complex and meticulous endeavor that involves careful selection of raw materials, precise design specifications, and rigorous quality control measures. Chip resistors play a vital role in modern electronics, enabling the functionality of countless devices we rely on daily. As the industry continues to innovate and adapt to emerging technologies, the future of chip resistors looks promising, with advancements in miniaturization, performance, and sustainability paving the way for even greater applications.
IX. References
A comprehensive list of academic journals, industry reports, and manufacturer guidelines can provide further insights into the chip resistor production process and its significance in the electronics industry.
What is the Mainstream Chip Resistor Production Process?
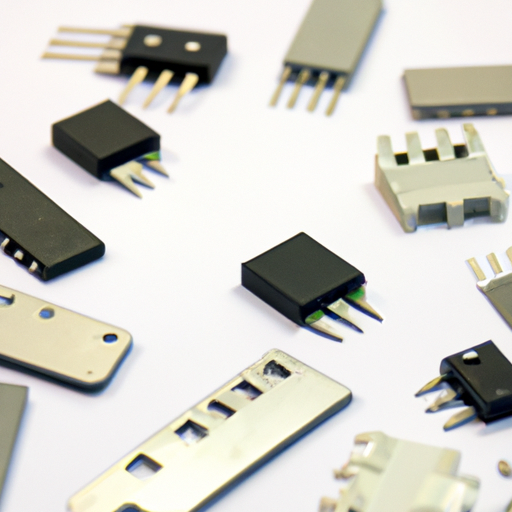
I. Introduction
Chip resistors, also known as surface mount resistors, are essential components in modern electronic circuits. These tiny devices play a crucial role in controlling the flow of electric current, ensuring that circuits function correctly and efficiently. As the demand for smaller, more efficient electronic devices continues to rise, understanding the production process of chip resistors becomes increasingly important. This blog post will provide an in-depth look at the mainstream chip resistor production process, from raw materials to innovations shaping the future of the industry.
II. Raw Materials
The production of chip resistors begins with the selection of high-quality raw materials. The primary materials used in chip resistors include ceramic substrates, metal films, and conductive pastes.
A. Types of Materials Used in Chip Resistors
1. **Ceramic Substrates**: Ceramic materials are favored for their excellent thermal stability and electrical insulation properties. They provide a robust base for the resistive elements and help maintain the integrity of the resistor under varying environmental conditions.
2. **Metal Films**: The resistive element in chip resistors is typically made from metal films, such as nickel-chromium or tantalum nitride. These materials are chosen for their precise resistance values and stability over time.
3. **Conductive Pastes**: Conductive pastes are used to create the electrical connections on the chip resistor. These pastes often contain a mixture of metal powders and binders, allowing for effective adhesion to the ceramic substrate.
B. Quality Control of Raw Materials
Quality control is critical in the production of chip resistors. Manufacturers must ensure that all raw materials meet stringent specifications to guarantee the performance and reliability of the final product. This involves rigorous testing and inspection of materials before they enter the production line.
C. Sourcing and Supply Chain Considerations
Sourcing high-quality raw materials is essential for maintaining production efficiency and product quality. Manufacturers often establish long-term relationships with suppliers to ensure a consistent supply of materials. Additionally, supply chain considerations, such as logistics and inventory management, play a vital role in the overall production process.
III. Design and Specifications
Before manufacturing can begin, it is essential to understand the design and specifications of chip resistors.
A. Understanding Resistor Specifications
1. **Resistance Value**: The resistance value is a critical specification that determines how much current will flow through the resistor. It is measured in ohms and can vary widely depending on the application.
2. **Tolerance**: Tolerance indicates the allowable deviation from the specified resistance value. It is typically expressed as a percentage and is crucial for applications requiring precise current control.
3. **Temperature Coefficient**: This specification describes how the resistance value changes with temperature. A low temperature coefficient is desirable for applications where temperature fluctuations are expected.
B. Design Considerations for Chip Resistors
1. **Size and Form Factor**: Chip resistors come in various sizes, and the choice of form factor depends on the specific application. Smaller resistors are often preferred for compact devices, while larger ones may be used in high-power applications.
2. **Power Rating**: The power rating indicates the maximum amount of power the resistor can dissipate without overheating. This specification is crucial for ensuring the reliability and longevity of the resistor.
C. Simulation and Modeling Techniques
Before moving to production, manufacturers often use simulation and modeling techniques to predict the performance of chip resistors under various conditions. This helps in optimizing the design and ensuring that the final product meets all specifications.
IV. Manufacturing Process
The manufacturing process of chip resistors involves several stages, each critical to producing a high-quality product.
A. Overview of the Production Stages
The production process can be broken down into several key stages, including substrate preparation, deposition of resistive material, sintering and curing, trimming and adjusting resistance values, application of protective coatings, and final inspection and testing.
B. Step-by-Step Breakdown of the Manufacturing Process
1. **Substrate Preparation**:
- **Cleaning and Surface Treatment**: The ceramic substrates undergo thorough cleaning to remove any contaminants that could affect adhesion and performance. Surface treatments may also be applied to enhance bonding.
- **Cutting and Shaping**: The substrates are cut and shaped into the desired dimensions, ensuring consistency across all units.
2. **Deposition of Resistive Material**:
- **Screen Printing**: A common method for applying the resistive material involves screen printing, where a stencil is used to deposit the metal film onto the substrate.
- **Thin-Film Deposition**: In some cases, thin-film deposition techniques, such as sputtering or evaporation, are used to create a uniform layer of resistive material.
3. **Sintering and Curing**:
- **Temperature Control**: The substrates are subjected to high temperatures in a controlled environment to sinter the resistive material, enhancing its electrical properties.
- **Time Management**: The duration of the sintering process is carefully monitored to ensure optimal results.
4. **Trimming and Adjusting Resistance Values**:
- **Laser Trimming**: This precise method involves using a laser to remove material from the resistive layer, allowing for fine-tuning of the resistance value.
- **Mechanical Trimming**: In some cases, mechanical methods may be employed to achieve the desired resistance.
5. **Application of Protective Coatings**:
- **Types of Coatings**: Various protective coatings, such as epoxy or silicone, are applied to enhance durability and protect against environmental factors.
- **Importance of Coatings for Durability**: These coatings are essential for ensuring the longevity of chip resistors, especially in harsh operating conditions.
6. **Final Inspection and Testing**:
- **Electrical Testing**: Each resistor undergoes rigorous electrical testing to verify its performance against specified parameters.
- **Visual Inspection**: A thorough visual inspection is conducted to identify any defects or inconsistencies in the manufacturing process.
V. Quality Control and Assurance
Quality control is a cornerstone of chip resistor production. Manufacturers implement strict testing methods and adhere to industry standards to ensure the reliability of their products.
A. Importance of Quality Control in Chip Resistor Production
Quality control helps prevent defects and ensures that each resistor meets the required specifications. This is particularly important in applications where failure could lead to significant consequences.
B. Testing Methods and Standards
1. **Reliability Testing**: Resistors are subjected to various stress tests to evaluate their performance under extreme conditions, such as high temperatures and humidity.
2. **Environmental Testing**: Environmental tests assess how resistors perform in different environmental conditions, ensuring they can withstand real-world applications.
C. Certification and Compliance with Industry Standards
Manufacturers often seek certification from recognized industry bodies to demonstrate compliance with established standards. This not only enhances credibility but also assures customers of the quality and reliability of the products.
VI. Packaging and Distribution
Once the chip resistors have passed all quality checks, they are prepared for packaging and distribution.
A. Packaging Methods for Chip Resistors
1. **Tape and Reel Packaging**: This method is commonly used for surface mount devices, allowing for easy handling and automated assembly in manufacturing processes.
2. **Bulk Packaging**: For certain applications, resistors may be packaged in bulk, providing flexibility for manufacturers who prefer to handle components individually.
B. Logistics and Distribution Channels
Efficient logistics and distribution channels are essential for ensuring that chip resistors reach customers in a timely manner. Manufacturers often work with logistics partners to optimize shipping and delivery processes.
C. Considerations for Global Markets
As the demand for chip resistors grows globally, manufacturers must consider various factors, such as regulatory compliance and market preferences, to successfully navigate international markets.
VII. Innovations and Future Trends
The chip resistor industry is continually evolving, driven by advancements in technology and changing market demands.
A. Advances in Chip Resistor Technology
1. **Miniaturization**: As electronic devices become smaller, the demand for miniaturized chip resistors has increased. Manufacturers are developing new techniques to produce smaller, more efficient resistors without compromising performance.
2. **Enhanced Performance Characteristics**: Innovations in materials and manufacturing processes are leading to chip resistors with improved performance characteristics, such as higher power ratings and better thermal stability.
B. Impact of Emerging Technologies
1. **IoT and Smart Devices**: The rise of the Internet of Things (IoT) and smart devices is driving demand for chip resistors that can support advanced functionalities while maintaining compact sizes.
2. **Automotive Applications**: The automotive industry is increasingly relying on chip resistors for various applications, including electric vehicles and advanced driver-assistance systems (ADAS).
C. Sustainability and Eco-Friendly Practices in Production
As environmental concerns grow, manufacturers are exploring sustainable practices in chip resistor production. This includes using eco-friendly materials and reducing waste throughout the manufacturing process.
VIII. Conclusion
In summary, the production process of chip resistors is a complex and meticulous endeavor that involves careful selection of raw materials, precise design specifications, and rigorous quality control measures. Chip resistors play a vital role in modern electronics, enabling the functionality of countless devices we rely on daily. As the industry continues to innovate and adapt to emerging technologies, the future of chip resistors looks promising, with advancements in miniaturization, performance, and sustainability paving the way for even greater applications.
IX. References
A comprehensive list of academic journals, industry reports, and manufacturer guidelines can provide further insights into the chip resistor production process and its significance in the electronics industry.