Common Production Processes for Stainless Steel Resistors
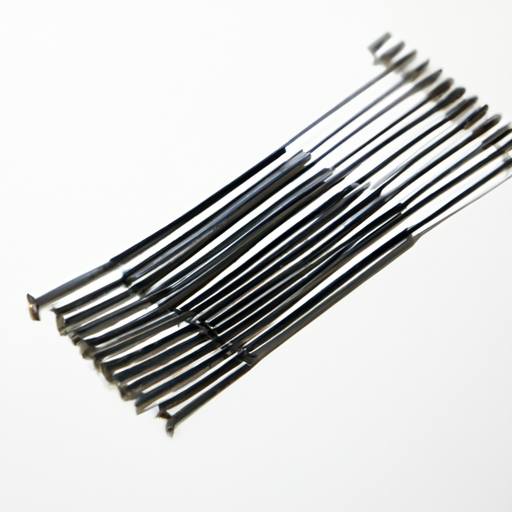
I. Introduction
Stainless steel resistors are essential components in electronic circuits, serving the critical function of controlling current flow and voltage levels. These resistors are made from stainless steel, a material known for its durability, corrosion resistance, and thermal stability. As technology advances, the demand for high-performance resistors has increased, leading to the development of sophisticated production processes. This blog post will explore the common production processes for stainless steel resistors, highlighting the materials used, design considerations, and innovations in manufacturing techniques.
II. Materials Used in Stainless Steel Resistors
A. Composition of Stainless Steel
Stainless steel is an alloy primarily composed of iron, chromium, and varying amounts of other elements such as nickel and molybdenum. The most common types of stainless steel used in resistor production are 304 and 316 grades.
Type 304: Known for its excellent corrosion resistance and good formability, Type 304 is often used in applications where moderate strength and resistance to oxidation are required.
Type 316: This grade offers superior corrosion resistance, particularly against chlorides and other aggressive environments, making it ideal for high-performance resistors.
The properties of stainless steel, such as its high melting point and resistance to thermal expansion, make it suitable for use in resistors, where stability and reliability are paramount.
B. Additional Materials and Coatings
In addition to stainless steel, various conductive and insulating materials are used in the production of resistors.
Conductive Materials: Carbon and metal films (such as nickel or copper) are often employed to create the resistive element. These materials are chosen for their electrical properties and compatibility with stainless steel.
Insulating Materials: Insulators are crucial for preventing unwanted current flow and ensuring the resistor functions correctly. Common insulating materials include ceramics and epoxy coatings, which provide electrical isolation and protection against environmental factors.
III. Design Considerations
A. Electrical Specifications
When designing stainless steel resistors, several electrical specifications must be considered:
Resistance Values: The desired resistance value is determined based on the application requirements. This can range from a few ohms to several megaohms.
Tolerance Levels: Tolerance indicates how much the actual resistance can vary from the specified value. Common tolerance levels for resistors are ±1%, ±5%, and ±10%.
B. Physical Dimensions
The physical dimensions of the resistor are also critical:
Size and Shape: Resistors can come in various shapes and sizes, depending on their intended use. Common forms include cylindrical, rectangular, and chip resistors.
Mounting Options: Resistors can be designed for different mounting methods, such as through-hole or surface mount, which affects their integration into electronic circuits.
C. Thermal Management
Effective thermal management is essential for resistor performance:
Heat Dissipation: Resistors generate heat during operation, and efficient heat dissipation is necessary to prevent overheating and ensure reliability.
Temperature Coefficients: The temperature coefficient of resistance (TCR) indicates how much the resistance changes with temperature. A low TCR is desirable for stable performance across varying temperatures.
IV. Common Production Processes
A. Material Preparation
The production of stainless steel resistors begins with material preparation:
1. **Sourcing and Quality Control**: High-quality stainless steel is sourced from reputable suppliers. Rigorous quality control measures are implemented to ensure the material meets industry standards.
2. **Cutting and Shaping Raw Materials**: The stainless steel is cut and shaped into the desired form using techniques such as laser cutting or CNC machining. This step is crucial for achieving precise dimensions and tolerances.
B. Resistor Element Fabrication
The next step involves fabricating the resistor element:
1. **Thin-Film Deposition**:
- **Sputtering**: This technique involves depositing a thin layer of conductive material onto the stainless steel substrate using a vacuum process. Sputtering allows for precise control over the thickness and uniformity of the film.
- **Chemical Vapor Deposition (CVD)**: CVD is another method for creating thin films, where gaseous precursors react on the substrate surface to form a solid film. This process is known for producing high-quality, uniform coatings.
2. **Thick-Film Printing**:
- **Screen Printing Techniques**: In this method, a paste containing conductive materials is printed onto the substrate through a mesh screen. This technique is suitable for creating thicker resistive elements.
- **Ink Formulation**: The formulation of the ink is critical, as it must provide the desired electrical properties while adhering well to the stainless steel surface.
C. Assembly Processes
Once the resistor elements are fabricated, the assembly process begins:
1. **Component Assembly**:
- **Joining Techniques**: Various joining techniques, such as soldering or welding, are used to connect the resistor elements to terminals or other components. The choice of technique depends on the design and application requirements.
- **Automated vs. Manual Assembly**: Many manufacturers employ automated assembly processes to enhance efficiency and consistency, although manual assembly may still be used for specialized applications.
2. **Encapsulation and Coating**:
- **Protective Coatings**: After assembly, resistors are often coated with protective materials to enhance durability and resistance to environmental factors.
- **Environmental Sealing**: Sealing techniques are employed to protect the resistor from moisture, dust, and other contaminants, ensuring long-term reliability.
D. Testing and Quality Control
Quality control is a critical aspect of resistor production:
1. **Electrical Testing**:
- **Resistance Measurement**: Each resistor undergoes electrical testing to verify its resistance value and tolerance. Automated testing equipment is often used for accuracy.
- **Load Testing**: Resistors are subjected to load testing to ensure they can handle the specified power levels without failure.
2. **Mechanical Testing**:
- **Durability and Stress Tests**: Mechanical tests assess the physical robustness of the resistors, ensuring they can withstand mechanical stress during operation.
- **Environmental Testing**: Resistors are tested under various environmental conditions, such as humidity and temperature extremes, to evaluate their performance and reliability.
V. Innovations in Production Techniques
A. Advances in Materials Science
Recent advancements in materials science have led to the development of new stainless steel alloys and enhanced conductive materials. These innovations improve the performance and reliability of stainless steel resistors, allowing for greater precision and efficiency in electronic circuits.
B. Automation and Industry 4.0
The rise of automation and Industry 4.0 has transformed resistor manufacturing:
Smart Manufacturing Processes: Manufacturers are increasingly adopting smart technologies, such as IoT devices and real-time monitoring systems, to optimize production efficiency and reduce waste.
Use of AI and Machine Learning: AI and machine learning algorithms are being utilized to analyze production data, predict maintenance needs, and improve quality control processes.
C. Sustainability Practices
Sustainability is becoming a key focus in resistor production:
Recycling of Materials: Many manufacturers are implementing recycling programs to reduce waste and promote the reuse of materials, including stainless steel and conductive elements.
Energy-Efficient Production Methods: Efforts are being made to adopt energy-efficient production techniques, minimizing the environmental impact of resistor manufacturing.
VI. Conclusion
In summary, the production processes for stainless steel resistors involve a complex interplay of material selection, design considerations, and advanced manufacturing techniques. From sourcing high-quality stainless steel to employing innovative fabrication methods, each step is crucial for ensuring the performance and reliability of these essential electronic components. Ongoing research and development in materials science, automation, and sustainability practices will continue to shape the future of resistor manufacturing, paving the way for more efficient and environmentally friendly production methods.
VII. References
- Academic journals and articles on materials science and resistor technology.
- Industry reports and white papers discussing advancements in resistor manufacturing.
- Manufacturer guidelines and specifications for stainless steel resistors.
This comprehensive overview of the common production processes for stainless steel resistors highlights the importance of each stage in creating reliable and efficient electronic components. As technology evolves, so too will the methods and materials used in resistor production, ensuring that these vital components meet the demands of modern electronics.
Common Production Processes for Stainless Steel Resistors
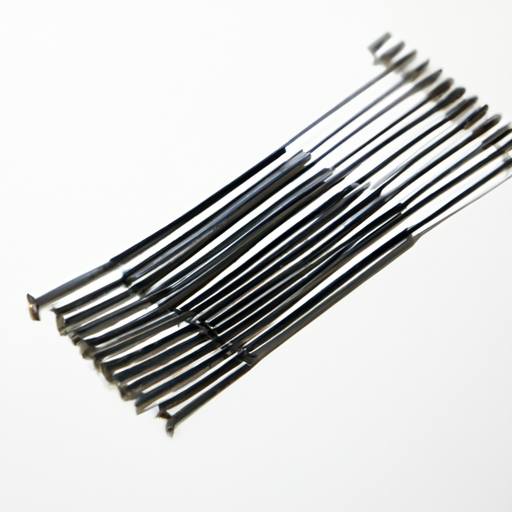
I. Introduction
Stainless steel resistors are essential components in electronic circuits, serving the critical function of controlling current flow and voltage levels. These resistors are made from stainless steel, a material known for its durability, corrosion resistance, and thermal stability. As technology advances, the demand for high-performance resistors has increased, leading to the development of sophisticated production processes. This blog post will explore the common production processes for stainless steel resistors, highlighting the materials used, design considerations, and innovations in manufacturing techniques.
II. Materials Used in Stainless Steel Resistors
A. Composition of Stainless Steel
Stainless steel is an alloy primarily composed of iron, chromium, and varying amounts of other elements such as nickel and molybdenum. The most common types of stainless steel used in resistor production are 304 and 316 grades.
Type 304: Known for its excellent corrosion resistance and good formability, Type 304 is often used in applications where moderate strength and resistance to oxidation are required.
Type 316: This grade offers superior corrosion resistance, particularly against chlorides and other aggressive environments, making it ideal for high-performance resistors.
The properties of stainless steel, such as its high melting point and resistance to thermal expansion, make it suitable for use in resistors, where stability and reliability are paramount.
B. Additional Materials and Coatings
In addition to stainless steel, various conductive and insulating materials are used in the production of resistors.
Conductive Materials: Carbon and metal films (such as nickel or copper) are often employed to create the resistive element. These materials are chosen for their electrical properties and compatibility with stainless steel.
Insulating Materials: Insulators are crucial for preventing unwanted current flow and ensuring the resistor functions correctly. Common insulating materials include ceramics and epoxy coatings, which provide electrical isolation and protection against environmental factors.
III. Design Considerations
A. Electrical Specifications
When designing stainless steel resistors, several electrical specifications must be considered:
Resistance Values: The desired resistance value is determined based on the application requirements. This can range from a few ohms to several megaohms.
Tolerance Levels: Tolerance indicates how much the actual resistance can vary from the specified value. Common tolerance levels for resistors are ±1%, ±5%, and ±10%.
B. Physical Dimensions
The physical dimensions of the resistor are also critical:
Size and Shape: Resistors can come in various shapes and sizes, depending on their intended use. Common forms include cylindrical, rectangular, and chip resistors.
Mounting Options: Resistors can be designed for different mounting methods, such as through-hole or surface mount, which affects their integration into electronic circuits.
C. Thermal Management
Effective thermal management is essential for resistor performance:
Heat Dissipation: Resistors generate heat during operation, and efficient heat dissipation is necessary to prevent overheating and ensure reliability.
Temperature Coefficients: The temperature coefficient of resistance (TCR) indicates how much the resistance changes with temperature. A low TCR is desirable for stable performance across varying temperatures.
IV. Common Production Processes
A. Material Preparation
The production of stainless steel resistors begins with material preparation:
1. **Sourcing and Quality Control**: High-quality stainless steel is sourced from reputable suppliers. Rigorous quality control measures are implemented to ensure the material meets industry standards.
2. **Cutting and Shaping Raw Materials**: The stainless steel is cut and shaped into the desired form using techniques such as laser cutting or CNC machining. This step is crucial for achieving precise dimensions and tolerances.
B. Resistor Element Fabrication
The next step involves fabricating the resistor element:
1. **Thin-Film Deposition**:
- **Sputtering**: This technique involves depositing a thin layer of conductive material onto the stainless steel substrate using a vacuum process. Sputtering allows for precise control over the thickness and uniformity of the film.
- **Chemical Vapor Deposition (CVD)**: CVD is another method for creating thin films, where gaseous precursors react on the substrate surface to form a solid film. This process is known for producing high-quality, uniform coatings.
2. **Thick-Film Printing**:
- **Screen Printing Techniques**: In this method, a paste containing conductive materials is printed onto the substrate through a mesh screen. This technique is suitable for creating thicker resistive elements.
- **Ink Formulation**: The formulation of the ink is critical, as it must provide the desired electrical properties while adhering well to the stainless steel surface.
C. Assembly Processes
Once the resistor elements are fabricated, the assembly process begins:
1. **Component Assembly**:
- **Joining Techniques**: Various joining techniques, such as soldering or welding, are used to connect the resistor elements to terminals or other components. The choice of technique depends on the design and application requirements.
- **Automated vs. Manual Assembly**: Many manufacturers employ automated assembly processes to enhance efficiency and consistency, although manual assembly may still be used for specialized applications.
2. **Encapsulation and Coating**:
- **Protective Coatings**: After assembly, resistors are often coated with protective materials to enhance durability and resistance to environmental factors.
- **Environmental Sealing**: Sealing techniques are employed to protect the resistor from moisture, dust, and other contaminants, ensuring long-term reliability.
D. Testing and Quality Control
Quality control is a critical aspect of resistor production:
1. **Electrical Testing**:
- **Resistance Measurement**: Each resistor undergoes electrical testing to verify its resistance value and tolerance. Automated testing equipment is often used for accuracy.
- **Load Testing**: Resistors are subjected to load testing to ensure they can handle the specified power levels without failure.
2. **Mechanical Testing**:
- **Durability and Stress Tests**: Mechanical tests assess the physical robustness of the resistors, ensuring they can withstand mechanical stress during operation.
- **Environmental Testing**: Resistors are tested under various environmental conditions, such as humidity and temperature extremes, to evaluate their performance and reliability.
V. Innovations in Production Techniques
A. Advances in Materials Science
Recent advancements in materials science have led to the development of new stainless steel alloys and enhanced conductive materials. These innovations improve the performance and reliability of stainless steel resistors, allowing for greater precision and efficiency in electronic circuits.
B. Automation and Industry 4.0
The rise of automation and Industry 4.0 has transformed resistor manufacturing:
Smart Manufacturing Processes: Manufacturers are increasingly adopting smart technologies, such as IoT devices and real-time monitoring systems, to optimize production efficiency and reduce waste.
Use of AI and Machine Learning: AI and machine learning algorithms are being utilized to analyze production data, predict maintenance needs, and improve quality control processes.
C. Sustainability Practices
Sustainability is becoming a key focus in resistor production:
Recycling of Materials: Many manufacturers are implementing recycling programs to reduce waste and promote the reuse of materials, including stainless steel and conductive elements.
Energy-Efficient Production Methods: Efforts are being made to adopt energy-efficient production techniques, minimizing the environmental impact of resistor manufacturing.
VI. Conclusion
In summary, the production processes for stainless steel resistors involve a complex interplay of material selection, design considerations, and advanced manufacturing techniques. From sourcing high-quality stainless steel to employing innovative fabrication methods, each step is crucial for ensuring the performance and reliability of these essential electronic components. Ongoing research and development in materials science, automation, and sustainability practices will continue to shape the future of resistor manufacturing, paving the way for more efficient and environmentally friendly production methods.
VII. References
- Academic journals and articles on materials science and resistor technology.
- Industry reports and white papers discussing advancements in resistor manufacturing.
- Manufacturer guidelines and specifications for stainless steel resistors.
This comprehensive overview of the common production processes for stainless steel resistors highlights the importance of each stage in creating reliable and efficient electronic components. As technology evolves, so too will the methods and materials used in resistor production, ensuring that these vital components meet the demands of modern electronics.