What is the Mainstream Varistor Production Process?
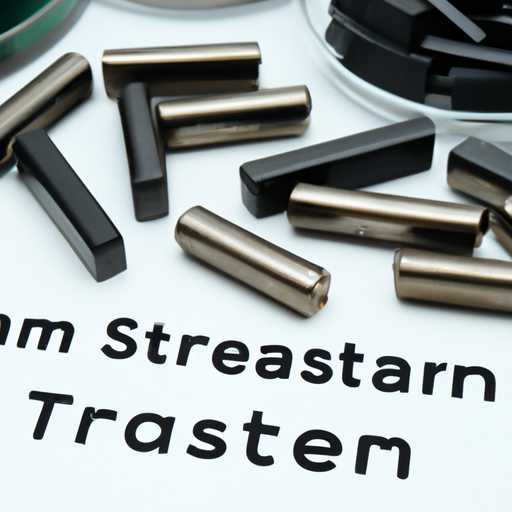
I. Introduction
Varistors, or voltage-dependent resistors, are crucial components in electrical circuits, providing protection against voltage surges and spikes. These devices play a significant role in safeguarding sensitive electronic equipment from damage caused by transient voltage events. The production process of varistors is intricate and involves several stages, each critical to ensuring the final product's performance and reliability. This blog post will explore the mainstream varistor production process, detailing the materials, methods, and quality control measures involved.
II. Understanding Varistors
A. Types of Varistors
Varistors are primarily categorized into two types: Zinc Oxide Varistors (ZOV) and Metal Oxide Varistors (MOV).
1. **Zinc Oxide Varistors (ZOV)**: These are the most common type of varistors, made primarily from zinc oxide. They exhibit excellent non-linear voltage-current characteristics, making them ideal for surge protection applications.
2. **Metal Oxide Varistors (MOV)**: MOVs are similar to ZOVs but may include other metal oxides in their composition. They are widely used in various applications due to their ability to handle high energy surges.
B. Applications of Varistors
Varistors are employed in numerous applications, including:
1. **Surge Protection**: They protect electronic devices from voltage spikes caused by lightning strikes or power surges.
2. **Voltage Regulation**: Varistors help maintain stable voltage levels in circuits, ensuring the safe operation of connected devices.
3. **Circuit Protection**: They prevent damage to sensitive components by clamping excessive voltage levels.
III. Raw Materials for Varistor Production
A. Key Materials Used
The production of varistors relies on several key materials:
1. **Zinc Oxide**: The primary component in ZOVs, zinc oxide is known for its excellent electrical properties.
2. **Other Metal Oxides**: Depending on the type of varistor, other metal oxides may be included to enhance performance.
3. **Additives and Binders**: These materials are used to improve the mechanical properties and processing characteristics of the varistor.
B. Quality Control of Raw Materials
Quality control begins with the sourcing and testing of raw materials. Ensuring the purity and consistency of materials is vital, as impurities can significantly affect the performance of the final product. Rigorous testing protocols are implemented to verify the quality of each component before production begins.
IV. The Varistor Production Process
The production of varistors involves several key steps:
A. Step 1: Material Preparation
The first step in the varistor production process is material preparation. This involves:
1. **Mixing of Raw Materials**: The raw materials, including zinc oxide and other metal oxides, are carefully mixed in precise proportions to achieve the desired electrical characteristics.
2. **Particle Size Reduction**: The mixed materials undergo particle size reduction to ensure uniformity and improve the sintering process's effectiveness.
B. Step 2: Shaping
Once the materials are prepared, the next step is shaping:
1. **Pressing Techniques**: The mixed materials are subjected to pressing techniques to form them into the desired shape, typically cylindrical or disc-like.
2. **Molding Processes**: In some cases, molding processes may be used to create more complex shapes, depending on the application requirements.
C. Step 3: Sintering
Sintering is a critical step in varistor production:
1. **Importance of Sintering**: This process involves heating the shaped materials to a temperature below their melting point, allowing particles to bond together and form a solid structure.
2. **Temperature and Atmosphere Control**: Precise control of temperature and atmosphere during sintering is essential to achieve the desired electrical properties and mechanical strength.
D. Step 4: Electrical Characterization
After sintering, the varistors undergo electrical characterization:
1. **Testing for Non-Linear Voltage-Current Characteristics**: This step involves testing the varistors to ensure they exhibit the expected non-linear voltage-current characteristics, which are crucial for their performance.
2. **Quality Assurance Measures**: Various quality assurance measures are implemented to verify that the varistors meet industry standards and specifications.
E. Step 5: Coating and Finishing
The final step in the production process is coating and finishing:
1. **Application of Protective Coatings**: Varistors are often coated with protective materials to enhance their durability and resistance to environmental factors.
2. **Final Inspection and Testing**: A thorough inspection and testing process is conducted to ensure that the finished varistors meet all quality and performance standards.
V. Quality Control in Varistor Production
A. Importance of Quality Control
Quality control is paramount in varistor production, as even minor defects can lead to significant failures in electrical circuits.
B. Testing Methods
To ensure the highest quality, various testing methods are employed:
1. **Electrical Testing**: This includes measuring the varistor's voltage-current characteristics and ensuring they align with specifications.
2. **Mechanical Testing**: Mechanical properties, such as strength and durability, are also assessed to ensure the varistors can withstand operational stresses.
C. Compliance with Industry Standards
Compliance with industry standards is essential for varistor manufacturers. Key standards include:
1. **International Electrotechnical Commission (IEC)**: This organization sets international standards for electrical and electronic products, including varistors.
2. **Underwriters Laboratories (UL)**: UL certification ensures that products meet safety and performance standards, providing assurance to manufacturers and consumers alike.
VI. Environmental Considerations
A. Waste Management in Varistor Production
The varistor production process generates waste materials that must be managed responsibly. Manufacturers are increasingly adopting waste management practices to minimize environmental impact.
B. Sustainable Practices
Sustainability is becoming a priority in varistor production:
1. **Recycling of Materials**: Efforts are being made to recycle materials used in production, reducing waste and conserving resources.
2. **Reducing Carbon Footprint**: Manufacturers are exploring ways to reduce their carbon footprint through energy-efficient processes and sustainable sourcing of materials.
VII. Future Trends in Varistor Production
A. Technological Advancements
The varistor production process is evolving with technological advancements:
1. **Automation in Manufacturing**: Automation is streamlining production processes, improving efficiency and consistency.
2. **Innovations in Material Science**: Ongoing research in material science is leading to the development of new materials that enhance varistor performance.
B. Market Demand and Growth
The demand for varistors is expected to grow due to:
1. **Increasing Need for Surge Protection**: As electronic devices become more prevalent, the need for effective surge protection solutions is rising.
2. **Emerging Applications in Renewable Energy**: Varistors are finding new applications in renewable energy systems, where they play a critical role in protecting sensitive components.
VIII. Conclusion
In summary, the mainstream varistor production process is a complex and multi-faceted operation that involves careful selection of raw materials, precise manufacturing techniques, and rigorous quality control measures. Varistors play a vital role in modern electronics, providing essential protection against voltage surges and ensuring the reliability of electrical circuits. As technology continues to advance and market demands evolve, the future of varistor manufacturing looks promising, with opportunities for innovation and growth.
IX. References
- Academic Journals
- Industry Reports
- Standards and Guidelines
This blog post provides a comprehensive overview of the varistor production process, highlighting its significance in the electronics industry and the ongoing advancements that shape its future.
What is the Mainstream Varistor Production Process?
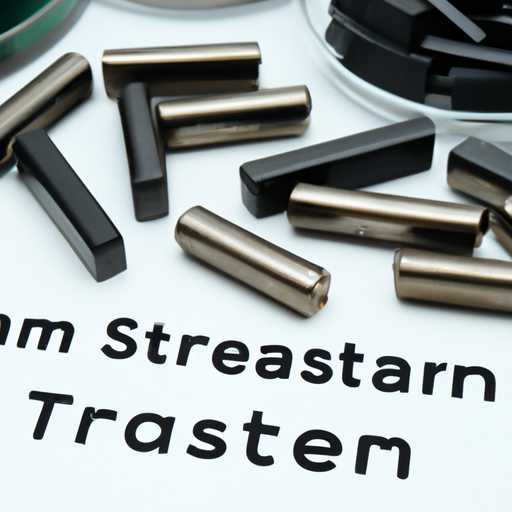
I. Introduction
Varistors, or voltage-dependent resistors, are crucial components in electrical circuits, providing protection against voltage surges and spikes. These devices play a significant role in safeguarding sensitive electronic equipment from damage caused by transient voltage events. The production process of varistors is intricate and involves several stages, each critical to ensuring the final product's performance and reliability. This blog post will explore the mainstream varistor production process, detailing the materials, methods, and quality control measures involved.
II. Understanding Varistors
A. Types of Varistors
Varistors are primarily categorized into two types: Zinc Oxide Varistors (ZOV) and Metal Oxide Varistors (MOV).
1. **Zinc Oxide Varistors (ZOV)**: These are the most common type of varistors, made primarily from zinc oxide. They exhibit excellent non-linear voltage-current characteristics, making them ideal for surge protection applications.
2. **Metal Oxide Varistors (MOV)**: MOVs are similar to ZOVs but may include other metal oxides in their composition. They are widely used in various applications due to their ability to handle high energy surges.
B. Applications of Varistors
Varistors are employed in numerous applications, including:
1. **Surge Protection**: They protect electronic devices from voltage spikes caused by lightning strikes or power surges.
2. **Voltage Regulation**: Varistors help maintain stable voltage levels in circuits, ensuring the safe operation of connected devices.
3. **Circuit Protection**: They prevent damage to sensitive components by clamping excessive voltage levels.
III. Raw Materials for Varistor Production
A. Key Materials Used
The production of varistors relies on several key materials:
1. **Zinc Oxide**: The primary component in ZOVs, zinc oxide is known for its excellent electrical properties.
2. **Other Metal Oxides**: Depending on the type of varistor, other metal oxides may be included to enhance performance.
3. **Additives and Binders**: These materials are used to improve the mechanical properties and processing characteristics of the varistor.
B. Quality Control of Raw Materials
Quality control begins with the sourcing and testing of raw materials. Ensuring the purity and consistency of materials is vital, as impurities can significantly affect the performance of the final product. Rigorous testing protocols are implemented to verify the quality of each component before production begins.
IV. The Varistor Production Process
The production of varistors involves several key steps:
A. Step 1: Material Preparation
The first step in the varistor production process is material preparation. This involves:
1. **Mixing of Raw Materials**: The raw materials, including zinc oxide and other metal oxides, are carefully mixed in precise proportions to achieve the desired electrical characteristics.
2. **Particle Size Reduction**: The mixed materials undergo particle size reduction to ensure uniformity and improve the sintering process's effectiveness.
B. Step 2: Shaping
Once the materials are prepared, the next step is shaping:
1. **Pressing Techniques**: The mixed materials are subjected to pressing techniques to form them into the desired shape, typically cylindrical or disc-like.
2. **Molding Processes**: In some cases, molding processes may be used to create more complex shapes, depending on the application requirements.
C. Step 3: Sintering
Sintering is a critical step in varistor production:
1. **Importance of Sintering**: This process involves heating the shaped materials to a temperature below their melting point, allowing particles to bond together and form a solid structure.
2. **Temperature and Atmosphere Control**: Precise control of temperature and atmosphere during sintering is essential to achieve the desired electrical properties and mechanical strength.
D. Step 4: Electrical Characterization
After sintering, the varistors undergo electrical characterization:
1. **Testing for Non-Linear Voltage-Current Characteristics**: This step involves testing the varistors to ensure they exhibit the expected non-linear voltage-current characteristics, which are crucial for their performance.
2. **Quality Assurance Measures**: Various quality assurance measures are implemented to verify that the varistors meet industry standards and specifications.
E. Step 5: Coating and Finishing
The final step in the production process is coating and finishing:
1. **Application of Protective Coatings**: Varistors are often coated with protective materials to enhance their durability and resistance to environmental factors.
2. **Final Inspection and Testing**: A thorough inspection and testing process is conducted to ensure that the finished varistors meet all quality and performance standards.
V. Quality Control in Varistor Production
A. Importance of Quality Control
Quality control is paramount in varistor production, as even minor defects can lead to significant failures in electrical circuits.
B. Testing Methods
To ensure the highest quality, various testing methods are employed:
1. **Electrical Testing**: This includes measuring the varistor's voltage-current characteristics and ensuring they align with specifications.
2. **Mechanical Testing**: Mechanical properties, such as strength and durability, are also assessed to ensure the varistors can withstand operational stresses.
C. Compliance with Industry Standards
Compliance with industry standards is essential for varistor manufacturers. Key standards include:
1. **International Electrotechnical Commission (IEC)**: This organization sets international standards for electrical and electronic products, including varistors.
2. **Underwriters Laboratories (UL)**: UL certification ensures that products meet safety and performance standards, providing assurance to manufacturers and consumers alike.
VI. Environmental Considerations
A. Waste Management in Varistor Production
The varistor production process generates waste materials that must be managed responsibly. Manufacturers are increasingly adopting waste management practices to minimize environmental impact.
B. Sustainable Practices
Sustainability is becoming a priority in varistor production:
1. **Recycling of Materials**: Efforts are being made to recycle materials used in production, reducing waste and conserving resources.
2. **Reducing Carbon Footprint**: Manufacturers are exploring ways to reduce their carbon footprint through energy-efficient processes and sustainable sourcing of materials.
VII. Future Trends in Varistor Production
A. Technological Advancements
The varistor production process is evolving with technological advancements:
1. **Automation in Manufacturing**: Automation is streamlining production processes, improving efficiency and consistency.
2. **Innovations in Material Science**: Ongoing research in material science is leading to the development of new materials that enhance varistor performance.
B. Market Demand and Growth
The demand for varistors is expected to grow due to:
1. **Increasing Need for Surge Protection**: As electronic devices become more prevalent, the need for effective surge protection solutions is rising.
2. **Emerging Applications in Renewable Energy**: Varistors are finding new applications in renewable energy systems, where they play a critical role in protecting sensitive components.
VIII. Conclusion
In summary, the mainstream varistor production process is a complex and multi-faceted operation that involves careful selection of raw materials, precise manufacturing techniques, and rigorous quality control measures. Varistors play a vital role in modern electronics, providing essential protection against voltage surges and ensuring the reliability of electrical circuits. As technology continues to advance and market demands evolve, the future of varistor manufacturing looks promising, with opportunities for innovation and growth.
IX. References
- Academic Journals
- Industry Reports
- Standards and Guidelines
This blog post provides a comprehensive overview of the varistor production process, highlighting its significance in the electronics industry and the ongoing advancements that shape its future.